Introduction
In the world of welding, having knowledge about various techniques is crucial.
It empowers welders to tackle different welding challenges effectively and efficiently.
The ability to adapt to different welding methods not only widens their skill set but also opens up new opportunities for their career.
Gaining an understanding of various welding techniques is incredibly beneficial for welders.
It allows them to choose the most suitable method for each project, ensuring high-quality and durable welds.
Different materials and joint designs require specific welding techniques, so being well-versed in multiple methods increases the chances of success.
Moreover, having knowledge about different welding techniques enhances a welder’s problem-solving skills.
They will be able to evaluate a welding situation and determine the most appropriate approach to achieve the desired results.
This expertise allows them to tackle complex welding projects confidently, ensuring customer satisfaction.
In their welding career, this knowledge can benefit welders in multiple ways. It can lead to increased job opportunities, as they can offer a wider range of welding services.
It also allows them to work on diverse projects in various industries, expanding their expertise and network.
Additionally, being proficient in different welding techniques can potentially lead to higher income and professional growth.
In short, understanding different welding techniques is of utmost importance in the welding profession.
It equips welders with the necessary skills to handle diverse projects and opens up new avenues for career advancement.
So, whether you’re a beginner or an experienced welder, investing time in learning and mastering different welding methods will undoubtedly yield long-term benefits.
Common Welding Techniques
Welding is a fundamental process used in various industries to join metal pieces together.
Different welding techniques are employed depending on the specific requirements of a project.
Here, we will discuss and define some of the most commonly used welding techniques, such as MIG, TIG, Stick, and Flux-Cored, and highlight their differences in terms of equipment, process, and applications.
We will also explore the advantages and disadvantages of each technique, and provide examples of industries or projects where they are commonly used.
MIG Welding
MIG (Metal Inert Gas) welding, also known as Gas Metal Arc Welding (GMAW), uses a continuous solid wire electrode that is fed through a welding gun.
The electrode is melted to form the weld, while an inert shielding gas protects the weld pool from atmospheric contamination.
MIG welding is widely used in automotive, construction, and manufacturing industries.
Advantages
- Fast and efficient process
- Suitable for a wide range of materials
- Produces clean and smooth welds
Disadvantages
- Requires a constant supply of shielding gas
- Limited in outdoor applications due to wind interference
TIG Welding
TIG (Tungsten Inert Gas) welding, also known as Gas Tungsten Arc Welding (GTAW), uses a non-consumable tungsten electrode to create the weld.
An inert shielding gas, usually argon, is used to protect the weld area from atmospheric contamination.
TIG welding is commonly used in aerospace, automotive, and artistic applications.
Unlock Your Career Potential
Visualize a clear path to success with our tailored Career Consulting service. Personalized insights in just 1-3 days.
Get StartedAdvantages
- Allows precise control over the weld
- Can be used on a variety of metals, including exotic alloys
- Produces high-quality welds with excellent aesthetic appearance
Disadvantages
- Requires high skill level and experience
- Slower than other welding techniques
- Not suitable for thick materials
Stick Welding
Stick welding, also known as Shielded Metal Arc Welding (SMAW), uses a flux-coated electrode that melts to create the weld.
The flux coating creates a protective layer over the weld, shielding it from atmospheric contamination.
This technique is commonly used in construction, maintenance, and repair projects.
Advantages
- Can weld on dirty or rusty metals
- Does not require shielding gas
- Portable and suitable for outdoor applications
Disadvantages
- Produces a rougher weld appearance
- Requires frequent changing of electrodes
- Not suitable for thin materials
Flux-Cored Welding
Flux-Cored welding is similar to MIG welding but uses a tubular wire filled with flux instead of a solid wire.
The flux creates a protective gas shield and provides additional control over the welding process.
This technique is commonly used in construction, shipbuilding, and heavy fabrication.
Advantages
- High deposition rates for faster welding
- Can be used on thick materials
- Suitable for outdoor applications
Disadvantages
- Produces more spatter compared to other techniques
- Requires proper ventilation due to the release of fumes
In fact, understanding different welding techniques is crucial in choosing the right method for a particular project.
MIG, TIG, Stick, and Flux-Cored welding each have their advantages and disadvantages, making them suitable for specific applications.
By considering the equipment, process, and industry examples provided, professionals can make informed decisions when it comes to selecting the appropriate welding technique.
Read: Creating a Pollinator Garden in Canada
MIG Welding Technique
What MIG welding stands for and its full name, Metal Inert Gas welding
MIG welding stands for Metal Inert Gas welding. It is a popular welding technique used in various industries.
Basic Process
In MIG welding, a continuous wire electrode is fed through a welding gun, which is powered by a welding machine.
The electrode is heated and melted by an electric arc, creating a weld pool on the workpiece.
Simultaneously, a shielding gas, such as argon or carbon dioxide, is released to protect the weld from atmospheric contamination.
The welder controls the wire feed speed, voltage, and the flow rate of the shielding gas to achieve the desired weld quality.
Key Features, Advantages, and Applications
- MIG welding offers high welding speeds, making it suitable for production and fabrication processes.
- It provides excellent control over the weld pool and allows for precise welding on different materials.
- MIG welding can be performed on various metals, including mild steel, stainless steel, and aluminum.
- It produces strong and durable welds with good aesthetic appeal, as the welding wire acts as a filler material.
- With MIG welding, there is minimal post-weld cleaning required, resulting in time and cost savings.
- The versatility of MIG welding makes it widely used in automotive, construction, and manufacturing industries.
- It is commonly utilized to fabricate structures, repair machinery, weld pipelines, and assemble metal components.
Tips and Best Practices
- Ensure the work area is clean, free from rust, grease, and other contaminants that can affect the weld quality.
- Properly set the welding parameters, including wire feed speed, voltage, and shielding gas flow rate, based on the material thickness and type.
- Maintain the correct distance between the welding gun and the workpiece to ensure proper arc stability and penetration.
- Use the correct welding technique, such as a push or pull motion, depending on the direction of the torch movement.
- Monitor the weld pool and adjust the travel speed accordingly to maintain the desired weld bead shape and size.
- Regularly check and clean the welding gun, wire feeder, and contact tip to prevent any obstructions that may affect the wire feed and gas flow.
- Inspect the welds for any defects, such as porosity, cracks, or incomplete fusion, and make necessary adjustments for improvement.
- Practice good safety measures, including wearing appropriate protective gear, working in a well-ventilated area, and following proper electrical safety precautions.
MIG welding is a versatile and widely used welding technique due to its efficiency, control, and ability to weld various materials.
By understanding the basic process and employing best practices, welders can achieve successful MIG welds consistently.
Read: Rock Gardens: A Canadian Landscaping Trend
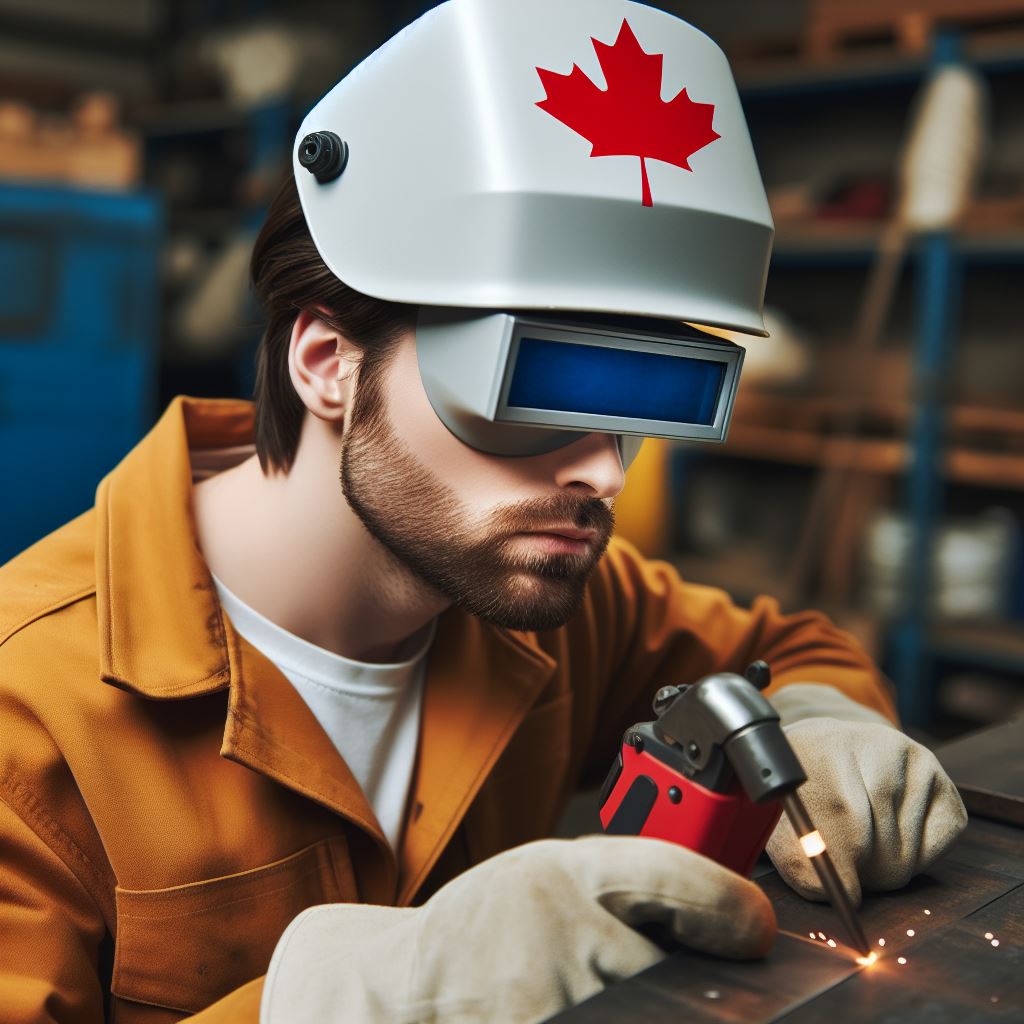
TIG Welding Technique
What is TIG welding?
TIG stands for Tungsten Inert Gas welding.
The basic process of TIG welding:
TIG welding involves a non-consumable tungsten electrode, a filler rod, and a shielding gas.
Key features of TIG welding
- TIG welding provides precise control, high-quality welds, and minimal spatter.
- It can be used with a wide range of metals, including stainless steel, aluminum, and copper.
- TIG welding produces clean and aesthetically pleasing welds.
Advantages of TIG welding
- TIG welding allows for welding thinner materials without distortion or burn-through.
- It offers excellent weld bead appearance, making it suitable for decorative or visual applications.
- TIG welding creates strong and durable welds with good integrity.
Applications of TIG welding
- TIG welding is commonly used in industries such as automotive, aerospace, and fabrication.
- It is ideal for welding critical joints, precision components, and tubes/pipes.
- TIG welding is also employed for artistic work, jewelry making, and sculpture fabrication.
Tips and best practices for successful TIG welds
- Ensure a clean and properly prepared work surface to achieve strong welds.
- Use the appropriate tungsten electrode and filler rod for the specific material being welded.
- Maintain a steady arc length, usually around 1/8 inch, for consistent heat control.
- Properly shield the weld area with the appropriate inert gas to prevent contamination.
- Take time to practice and develop your hand-eye coordination and welding technique.
- Be aware of the material’s thickness and adjust welding parameters accordingly.
- Regularly inspect and clean the tungsten electrode to maintain its effectiveness.
- Use proper personal protective equipment, including a welding helmet, gloves, and safety glasses.
- Ensure proper ventilation in the welding area to minimize exposure to fumes and gases.
- Seek guidance from experienced welders or consider taking professional welding courses.
In essence, TIG welding, also known as Tungsten Inert Gas welding, is a versatile and precise welding technique.
It offers numerous advantages such as high-quality welds, minimal spatter, and the ability to weld a wide range of materials.
TIG welding finds applications in various industries and is favored for its clean and aesthetically pleasing welds.
By following the tips and best practices for achieving successful TIG welds, welders can enhance their skills and produce strong and durable welds.
Read: Landscaping Safety: A Canadian Perspective
Stick Welding Technique
Stick welding, also known as Shielded Metal Arc Welding (SMAW)
- Stick welding, technically called Shielded Metal Arc Welding (SMAW), is a welding technique that uses an electrode coated in flux.
- Stick welding involves creating an electric arc between the coated electrode and the base material to join metals together.
The basic process of Stick welding
- In Stick welding, the electrode, which is coated in flux, is connected to the welding machine’s positive terminal.
- The welding machine’s negative terminal is connected to the workpiece or the metal to be welded.
- When the electrode makes contact with the metal, an electric arc is formed, which generates intense heat.
- This heat melts the base metal and the electrode, creating a weld pool.
- The flux coating on the electrode vaporizes, creating a shielding gas that protects the weld pool from atmospheric contamination.
- The molten metal from the electrode fills the gap between the metals being joined, creating a solid bond.
Key features, advantages, and applications of Stick welding
- Stick welding is versatile and can be used to weld various types of metals, including carbon steel, stainless steel, and cast iron.
- It is a portable welding process that can be performed in various positions, making it suitable for both indoor and outdoor applications.
- Stick welding is a cost-effective method as it requires minimal equipment and can be done using inexpensive electrodes.
- It provides good penetration and can produce strong welds that are resistant to corrosion.
- Stick welding is commonly used in construction, maintenance and repair, pipelines, and structural steel industries.
Safety precautions and considerations for Stick welding
- Wear appropriate personal protective equipment (PPE) such as welding helmets, gloves, and flame-resistant clothing.
- Ensure proper ventilation in the welding area to avoid exposure to harmful fumes and gases.
- Inspect welding equipment and electrodes for any defects or damage before starting the process.
- Securely ground the workpiece and welding machine to prevent electrical shocks.
- Keep a fire extinguisher nearby to extinguish any potential fires caused by sparks or heat.
- Follow proper electrode handling and storage procedures to prevent injuries and maintain electrode performance.
Stick welding stands out for its versatility, cost-effectiveness, and capability to create robust welds, making it a widely embraced technique.
By following proper safety precautions, welders can ensure a safe and successful Stick welding process.
Read: Canadian Landscape Design: Historical View
Flux-Cored Welding Technique
Flux-Cored welding is a technique similar to MIG welding but with some differences.
It involves the use of a tubular wire filled with flux and optional shielding gas.
What is Flux-Cored Welding?
Flux-Cored welding is a process that uses a continuously fed electrode wire with flux in its core.
The core flux melts during welding to create a shielding gas, protecting the weld pool from contaminants.
Similarities and Differences to MIG Welding:
- Similar to MIG welding, Flux-Cored welding is a semi-automatic process.
- The primary distinction lies in the choice of electrode utilized. Flux-Cored welding uses a tubular wire filled with flux instead of a solid wire.
The Basic Process of Flux-Cored Welding
Flux-Cored welding involves the following steps:
- The electrode wire with flux is fed through the welding gun.
- The power source provides the necessary electrical current for welding.
- The arc forms between the electrode wire and the workpiece.
- The heat from the arc melts the electrode wire and the flux in its core.
- The molten metal from the electrode forms the weld bead.
- The flux in the core also melts and creates a shielding gas to protect the weld pool.
- As the weld cools, the flux solidifies and forms a slag layer on the weld bead.
Key Features, Advantages, and Applications of Flux-Cored Welding
Flux-Cored welding offers several key features, advantages, and applications:
- Higher deposition rates compared to MIG welding, resulting in faster welding speeds.
- Excellent penetration, making it suitable for welding thick materials.
- Less sensitive to windy conditions, making it versatile for outdoor applications.
- Offers versatility for various applications, allowing usage with or without shielding gas as needed.
- Ideal for welding in construction, shipbuilding, and heavy equipment industries.
- Effective for joining dissimilar metals, such as mild steel and stainless steel.
Tips and Best Practices for Successful Flux-Cored Welds
To achieve successful Flux-Cored welds, consider the following tips and best practices:
- Choose the right flux type and wire diameter for the material and thickness you’re welding.
- Ensure proper wire feeding to prevent wire jamming or birdnesting.
- Maintain a consistent travel speed to achieve uniform bead appearance and prevent excessive heat buildup.
- Clean the workpiece to remove any contaminants that could affect the quality of the weld.
- Properly adjust welding parameters, including voltage, current, and wire feed speed.
- Use personal protective equipment, including a welding helmet, gloves, and protective clothing.
By understanding Flux-Cored welding and applying the right techniques, you can achieve high-quality welds for various applications in different industries.
Conclusion
Understanding diverse welding techniques is crucial for those involved in the welding industry.
By familiarizing themselves with various methods, welders can choose the most appropriate technique for each project.
The importance of this knowledge lies in its potential to make or break the quality and durability of welds.
Furthermore, understanding different welding techniques can enhance productivity and efficiency in welding operations.
It allows welders to work with different materials and overcome challenges that may arise during the welding process.
Welders should not limit themselves to the methods discussed but actively explore and learn more.
Expanding welding knowledge opens up opportunities to work on diverse projects and broaden one’s skillset.
Improving welding skills can give individuals a competitive edge in the job market, leading to better career prospects.
In a swiftly changing industry, possessing proficiency in diverse welding techniques is advantageous.
Developing expertise in less common techniques can set welders apart and attract niche job opportunities.
Understanding different welding techniques is highly beneficial for welders in the competitive job market.
By continuously expanding their welding knowledge, individuals can stay at the forefront of their profession.
I encourage readers to share their experiences and ask questions to foster a vibrant and supportive welding community.