Overview of Welding Techniques Used in Metal Fabrication
MIG Welding
MIG welding, or Gas Metal Arc Welding, employs a continuous wire feed.
This technique produces a strong bond between metals with high efficiency.
It is widely used in the automotive industry for its speed and versatility.
Moreover, MIG welding adapts well to various materials, including aluminum and steel.
As a result, it is a preferred choice for many fabricators.
TIG Welding
TIG welding, or Gas Tungsten Arc Welding, uses a non-consumable tungsten electrode.
This method allows for more control over the weld pool.
Its precision makes it ideal for thin materials and intricate designs.
Furthermore, TIG welding produces clean and high-quality welds.
This technique is commonly applied in aerospace and artistic metal fabrication.
Stick Welding
Stick welding, known as Shielded Metal Arc Welding, utilizes a consumable electrode.
This method is straightforward and cost-effective, making it accessible.
It works well in outdoor conditions where wind may affect other techniques.
However, stick welding requires skill to achieve a polished finish.
It remains popular among construction workers and maintenance crews.
Flux-Cored Arc Welding
Flux-cored arc welding operates similarly to MIG welding but with a tubular wire filled with flux.
This provides better protection against contamination during the welding process.
Moreover, it is effective for welding thicker materials and in windy environments.
Its efficiency and speed cater to high-production applications.
Consequently, it’s favored in heavy industries like shipbuilding and structural fabrication.
Submerged Arc Welding
Submerged arc welding involves a continuously fed electrode beneath a blanket of flux.
This technique generates minimal spatter, resulting in a clean workspace.
It is particularly suitable for large-scale welding projects in shipyards.
Additionally, submerged arc welding can produce deeper penetration welds.
Overall, it remains a preferred technique in heavy manufacturing sectors.
Unlock Your Career Potential
Visualize a clear path to success with our tailored Career Consulting service. Personalized insights in just 1-3 days.
Get StartedLaser Welding
Laser welding uses focused beams of light to melt and fuse materials together.
This advanced technique ensures high precision, especially for thin workpieces.
It minimizes heat-affected zones, reducing the chance of warping.
Moreover, laser welding enables faster processing times compared to traditional methods.
It finds extensive use in industries such as electronics and medical equipment.
Essential Welding Skills for Beginners
Understanding Welding Basics
Welding is an essential skill in metal fabrication.
It involves joining two pieces of metal together using heat and pressure.
Beginners must familiarize themselves with various welding techniques.
Each technique offers unique advantages and applications.
Safety Awareness and Practices
Prioritizing safety is crucial for anyone new to welding.
Wear appropriate protective gear, such as helmets, gloves, and aprons.
Always work in a well-ventilated area to avoid harmful fumes.
Understand how to handle equipment safely to prevent accidents.
Mastering Welding Techniques
Beginners should start with basic welding techniques.
For instance, MIG welding is user-friendly and versatile.
TIG welding offers precision for detailed work and thin materials.
Stick welding is excellent for outdoor work and various metals.
Learning to Read Blueprints
Understanding blueprints is vital for metal fabricators.
Blueprints provide necessary details about dimensions and designs.
Practice interpreting different symbols and specifications used in welding.
This knowledge enhances your accuracy and efficiency in projects.
Developing Metalworking Skills
Welding requires solid fundamental metalworking skills.
Learn to use tools such as grinders, cutters, and hammers.
Familiarity with different metals is equally important.
Each metal type has unique properties impacting the welding process.
Practicing Hands-On Techniques
Consistent practice is essential in mastering welding skills.
Start with smaller projects to build confidence.
As skills improve, gradually tackle more complex tasks.
Seek feedback from more experienced welders to refine your techniques.
Safety Practices and Equipment for Welders
Importance of Safety in Welding
Welding involves significant hazards, making safety crucial.
Unsafe practices can lead to serious injuries or accidents.
Proper safety measures protect welders and their coworkers.
Personal Protective Equipment
Welders should always wear appropriate personal protective equipment (PPE).
This includes helmets with suitable filters to protect their eyes.
Additionally, gloves should be abrasion-resistant and heat-proof.
Protective clothing must be flame-resistant and cover all skin.
Finally, steel-toed boots offer additional foot protection.
Ventilation and Fume Control
Effective ventilation is essential to maintain air quality.
Welders should work in areas with adequate airflow.
Fume extraction systems can help reduce harmful exposure.
Regardless, they must monitor for any toxic gas release.
Safe Workspace Practices
Organizing the workspace enhances safety during welding operations.
Welders should keep flammable materials away from welding areas.
Regularly inspecting tools and equipment is essential for safety.
Establishing clear communication among team members promotes awareness.
Emergency Procedures
Every welding facility should have an emergency plan in place.
Welders need to know how to respond to accidental injuries.
Training in first aid can save lives during emergencies.
Reporting accidents promptly ensures proper investigation and follow-up.
Regular Training and Certification
Welders should participate in regular safety training sessions.
Staying updated on best practices reduces workplace risks.
Certification programs enhance skills and safety knowledge.
Employers benefit from reduced accidents and higher productivity.
Uncover the Details: Exploring the Role of Metal Fabricators in Canada
Understanding Different Types of Welding Machines and Tools
Overview of Welding Machines
Welding machines are essential for metal fabricators.
These machines create a strong bond between metal pieces.
Different types of welding machines exist for various applications.
Understanding these machines helps in choosing the right one.
MIG Welding Machines
MIG welding machines are popular for their ease of use.
MIG stands for Metal Inert Gas welding.
These machines use a spool of wire as an electrode.
Additionally, they provide a continuous feed during welding.
MIG is suitable for thin and thick materials alike.
Many fabricators prefer MIG for its versatility.
TIG Welding Machines
TIG welding machines offer precision and control.
TIG stands for Tungsten Inert Gas welding.
These machines use a non-consumable tungsten electrode.
They are ideal for intricate work and thin metals.
Moreover, TIG welding produces high-quality welds.
However, it requires more skill than MIG welding.
Stick Welding Machines
Stick welding machines are among the oldest types available.
This method uses a consumable electrode coated in flux.
It is effective for outdoor work and windy conditions.
Stick welding is also affordable and widely accessible.
Many fabricators use it for heavy-duty applications.
Plasma Cutting Tools
Plasma cutting tools are essential for cutting metals.
These tools utilize a high-velocity jet of ionized gas.
Plasma cutting allows for precise and clean cuts.
Moreover, it can be used on various metal types.
This tool complements welding by preparing materials.
Welding Accessories and Safety Equipment
Using the right accessories enhances welding performance.
Welding helmets protect eyes from harmful sparks and UV rays.
Gloves provide protection and enhance grip during welding.
Welding jackets prevent burns and protect skin.
Furthermore, having a welding cart helps in organization.
Common Welding Tools
Several tools are essential for successful welding projects.
- Chipping hammers help remove slag from welds.
- Wire brushes clean metal surfaces before welding.
- Ground clamps ensure a strong electrical connection.
- Measuring tools assist in precise layout work.
Having these tools available improves efficiency and safety.
Uncover the Details: Best Practices for Precision in Metal Fabrication Work
The Role of Welding Certifications in Career Advancement
Importance of Welding Certifications
Welding certifications validate a welder’s skills and knowledge.
These certifications enhance job prospects significantly.
Employers often prioritize certified welders over non-certified individuals.
Additionally, certificates demonstrate a commitment to the profession.
As a result, certified welders can command higher salaries.
Types of Welding Certifications
Several organizations offer various welding certifications.
For example, the American Welding Society (AWS) provides numerous programs.
These programs include Certified Welder (CW) and Certified Welding Inspector (CWI).
Moreover, the National Center for Construction Education and Research (NCCER) also offers certifications.
Each certification focuses on different welding processes and techniques.
Impact on Career Opportunities
Having a certification opens doors to various career paths.
Certified welders can work in manufacturing, construction, and aerospace industries.
Many employers consider certifications a requirement for advanced positions.
Furthermore, certified professionals often experience greater job stability.
They can adapt to different roles, enhancing their employability.
Continuous Education and Skill Improvement
Welding certifications require ongoing education to stay relevant.
Welders must keep up with technological advancements in the field.
Participating in workshops and additional courses is essential.
Thus, continuous learning helps welders sharpen their skills.
Ultimately, this commitment benefits both professionals and employers.
Delve into the Subject: Tips for Maintaining HVAC Systems Like a Pro
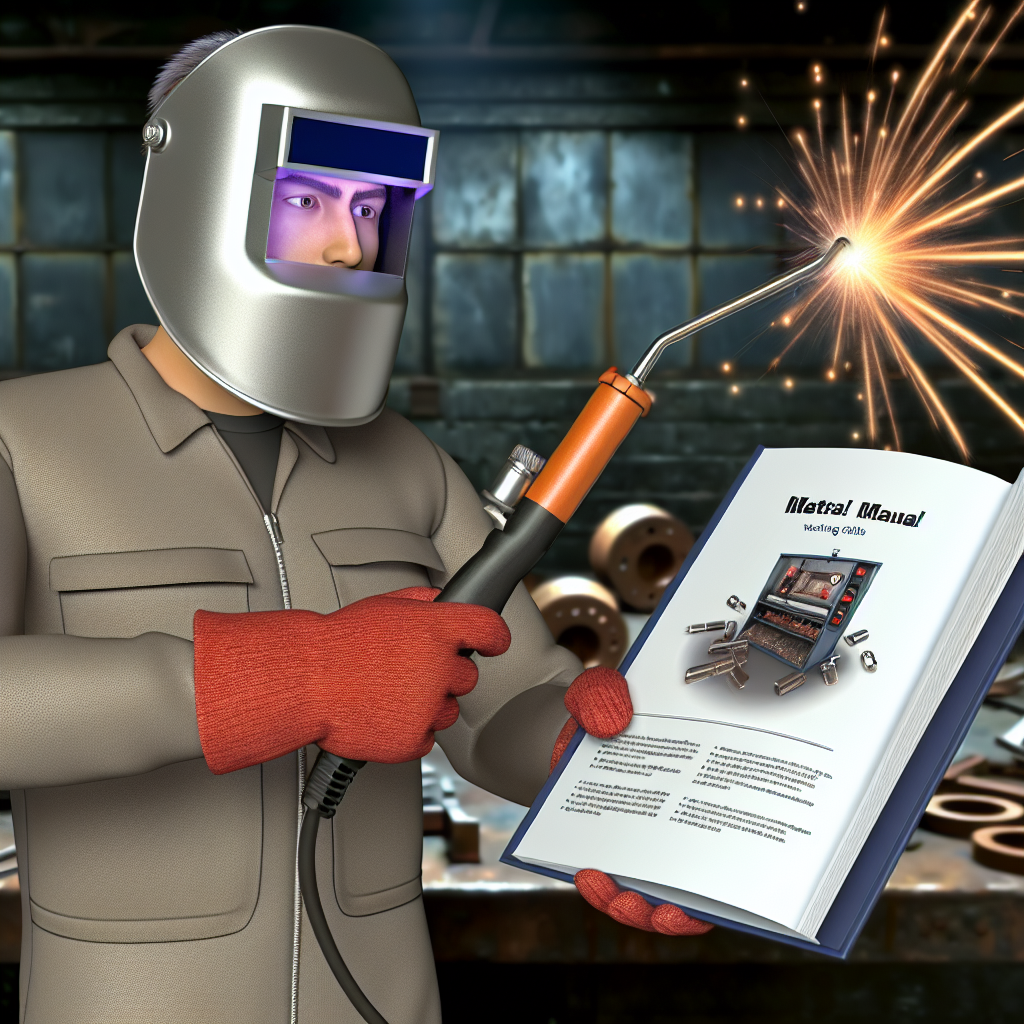
Common Welding Defects and How to Avoid Them
Introduction to Welding Defects
Welding defects often compromise the integrity of metal structures.
Understanding these defects is crucial for every metal fabricator.
This knowledge helps ensure high-quality welds and durable products.
Pore Formation
Pore formation is a common welding defect that leads to weak joints.
Gases can become trapped in the weld pool, causing voids.
To avoid this, ensure proper gas coverage during welding.
Additionally, maintain the right temperature and clean surfaces before welding.
Cracking
Cracking can occur due to thermal stresses or improper material selection.
It is essential to use materials compatible with your welding process.
Preheating the base metal can also minimize the risk of cracking.
Monitor cooling rates carefully to prevent brittle fracture.
Inconsistency in Weld Beads
Inconsistent weld beads can arise from poor technique or equipment issues.
To achieve uniform beads, maintain a steady travel speed.
Additionally, control the angle and distance of the welding torch.
Regularly check equipment calibration to ensure optimal performance.
Undercutting
Undercutting happens when the weld pool erodes the base metal.
This defect weakens the weld joint significantly.
Prevent undercutting by adjusting your travel speed and heat settings.
Ensure adequate filler material is used during the welding process.
Incomplete Fusion
Incomplete fusion occurs when the weld metal does not fuse properly with the base metal.
This defect often results from inadequate heat or poor cleaning.
Ensure both surfaces are free of contaminants before welding.
Use appropriate heat settings to melt the material effectively.
Implications of Understanding Welding Defects
Being aware of these common welding defects is instrumental for fabricators.
Taking proactive measures reduces the likelihood of defects.
Ultimately, this leads to stronger and more reliable metal products.
Uncover the Details: Understanding the Daily Tasks of an HVAC Technician
Materials Science: How Different Metals Affect Welding Processes
The Importance of Understanding Metals
Each metal possesses unique properties that influence welding methods.
Knowing these properties is vital for successful welding outcomes.
Additionally, the type of metal can determine the welding techniques to use.
Common Metals in Welding
Steel is one of the most widely used metals in welding.
This metal has excellent tensile strength and durability.
Aluminum, on the other hand, is lightweight and resistant to corrosion.
It requires different welding techniques compared to steel.
Copper is another popular metal, known for its excellent conductivity.
Metal Properties Affecting Welding
Metals differ in conductivity, melting points, and thermal expansion.
These variations can impact the welding process directly.
For instance, metals with higher thermal conductivity may require specific techniques.
Furthermore, the melting point influences the choice of filler materials.
Welding Techniques Based on Metal Types
Metals can be welded using various techniques, including MIG and TIG.
MIG welding is suitable for thin materials like aluminum.
TIG welding excels in producing clean, precise welds in stainless steel.
Understanding the right technique increases efficiency and quality.
Challenges in Welding Different Metals
Welding dissimilar metals presents unique challenges.
For example, combining steel and aluminum requires careful consideration.
Incompatible properties can lead to joint failure.
It is essential to choose the right filler metal to address these issues.
Future Trends in Metal Welding
Advancements in materials science continue to impact welding practices.
New alloys and composites are being developed for enhanced performance.
These materials often exhibit improved weldability and resistance.
Staying informed about these developments is crucial for fabricators.
The Importance of Continuous Learning and Skills Development in Welding
Adapting to Industry Changes
The welding industry constantly evolves with new technologies.
Fabricators must adapt to these changes to remain competitive.
Continuous learning ensures they stay updated on trends.
This adaptation helps improve job performance and efficiency.
Enhancing Job Opportunities
Investing in skills development opens new job prospects.
Employers value workers who pursue professional growth.
Employees with diverse skills often earn higher wages.
Furthermore, they can pursue leadership roles within organizations.
Improving Safety Standards
Ongoing training promotes awareness of safety measures.
Manufacturers regularly update safety protocols and regulations.
Understanding these changes reduces workplace accidents.
Ultimately, a safer work environment benefits everyone.
Fostering Innovation
Continuous learning encourages creative problem-solving.
Welders can apply new techniques to complex projects.
This innovation sets companies apart from their competitors.
Moreover, it leads to enhanced customer satisfaction.
Building Professional Networks
Learning opportunities often create valuable connections.
Networking can lead to collaboration and mentorship.
These relationships may help in job searches or career advancements.
Additionally, they encourage knowledge sharing among peers.