Introduction
Let’s explore robotic welding: Canada’s industrial future.
Robotics welding technologies are playing a crucial role in shaping Canada’s industrial future.
With the growing adoption of automated welding systems, various industries in Canada are experiencing increased productivity and efficiency gains.
“In an era defined by rapid technological advancements, Canada’s industrial sector stands at the crossroads of innovation with the advent of robotic welding.
This sophisticated fusion of robotics and welding techniques promises to revolutionize the way we conceive and execute industrial processes.
As the nexus between automation and craftsmanship, robotic welding not only amplifies efficiency but also elevates the precision and quality of manufacturing outputs.
Canada, known for its proclivity towards technological integration, is positioning itself as a global leader in industrial automation by embracing robotic welding as a cornerstone of its industrial future.
This shift is not merely about adopting cutting-edge technology but signifies a strategic move towards sustainable, scalable, and forward-thinking manufacturing practices.
The implications of this technological marriage extend beyond the factory floor, permeating the very fabric of Canada’s economic landscape.
From increased production rates and reduced operational costs to enhanced workplace safety and a surge in product innovation, the impact of robotic welding is reshaping the traditional contours of industrial operations.
In this comprehensive exploration, we embark on a journey to unravel the multifaceted dimensions of it in Canada.
We will delve into the nuances of its applications across diverse industries, examine the evolving skill sets demanded by this technological wave, and forecast the trajectory of careers in an era where man and machine collaborate seamlessly.
Join us as we navigate the realms of robotic welding, unveiling its transformative influence on Canada’s industrial present and sculpting a vision for an even more advanced and efficient future.”
Benefits of Robotic Welding
The advantages of using robotic welding systems in industrial applications
Robotic welding systems offer a range of advantages when it comes to industrial applications.
Here are some key benefits:
Improved Precision
- It systems are highly precise, ensuring accurate and consistent welds every time.
- They have advanced vision systems that can detect and compensate for variations in material and position.
- These systems eliminate the margin of error caused by human welders, resulting in higher quality welds.
- By maintaining consistent weld quality, it reduces the need for rework or repairs, saving time and costs.
Increased Productivity
- It systems have faster welding speeds compared to manual welding, resulting in increased productivity.
- They can work continuously without fatigue or breaks, leading to higher output and reduced downtime.
- Multiple robots can be used simultaneously, allowing for simultaneous welding of different parts, further speeding up the process.
- With the ability to weld complex shapes and perform multiple welding operations, these systems optimize production efficiency.
Enhanced Safety
- It improves worker safety by reducing their exposure to hazardous welding environments.
- It eliminates the need for manual welders to work in potentially dangerous conditions like high temperatures, fumes, or radiation.
- Advanced safety features, such as protective barriers and sensors, ensure that operators are protected from accidents.
- By automating welding tasks, robotic systems also reduce the risk of welder fatigue, which can contribute to workplace accidents.
Cost Savings
- Despite the initial investment, it systems can lead to significant cost savings in the long run.
- The increased precision and reduced need for rework or repairs result in less material wastage and lower production costs.
- These systems have a higher welding speed, allowing manufacturers to meet tight deadlines and reduce labor costs.
- Improved productivity and efficiency also lead to more competitive pricing, giving businesses a competitive edge.
Flexibility and Adaptability
- It systems can be programmed to weld a wide range of materials and complex shapes.
- They can easily adapt to changes in production requirements or switch between different welding tasks.
- With various end-effectors and tools available, these systems can handle different welding techniques and joint configurations.
- The flexibility of robotic welding systems allows manufacturers to respond quickly to market demands and optimize production processes.
In short, the benefits of robotic welding systems in industrial applications are undeniable.
They offer improved precision, increased productivity, enhanced safety, cost savings, and flexibility.
As technology continues to advance, these systems will play a crucial role in shaping Canada’s industrial future.
Read: Welding in the Canadian Oil and Gas Sector
Adoption of Robotic Welding in Canadian Industries
Robotic welding technology has gained significant adoption in various industries across Canada.
Examples of industries in Canada that have embraced robotic welding technology
Let’s explore some examples of sectors that have embraced this advanced technology:
Automotive Industry
The automotive sector in Canada has widely embraced robotic welding systems.
Companies like General Motors and Ford have integrated automated welding processes into their manufacturing lines to improve efficiency and product quality.
It systems allow manufacturers to weld components with precision, ensuring consistent quality and reducing the risk of defects.
These systems also enhance the speed of production, enabling automotive companies to meet high demand efficiently.
Unlock Your Career Potential
Visualize a clear path to success with our tailored Career Consulting service. Personalized insights in just 1-3 days.
Get StartedAerospace Industry
The aerospace industry has also witnessed the adoption of robotic welding technology.
Companies such as Bombardier Aerospace and Pratt & Whitney Canada utilize automated welding systems to fabricate aircraft components.
It offers a higher level of accuracy and repeatability, which is critical in the aerospace industry to ensure the structural integrity of aircraft parts.
Robotic systems excel in handling complex welding tasks, making them indispensable in aerospace manufacturing.
Manufacturing Sector
Within the broader manufacturing sector, numerous sub-industries have integrated robotic welding systems. These include steel fabrication, metalworking, and machinery manufacturing companies.
For instance, steel fabrication companies rely on robotic welding to join steel beams, plates, and other components with precision.
The use of robots increases productivity and reduces the consumption of both time and resources.
Manufacturers in the metalworking industry employ robotic welders to create intricate metal structures, such as gates and fences, with consistent accuracy.
The automation of welding processes enhances productivity and allows companies to meet customer demands efficiently.
Benefits of Robotic Welding in Canadian Industries
The integration of robotic welding systems has brought numerous benefits to Canadian industries:
- Increased Efficiency: It systems perform repetitive welding tasks at a higher speed than manual welders, resulting in increased productivity.
- Improved Quality: Robots offer precise and consistent welds, reducing the occurrence of defects and ensuring high product quality.
- Enhanced Safety: It reduces the risk of accidents and injuries to human workers, as they are shielded from hazardous welding processes.
- Cost Savings: While initial investment in robotic systems can be significant, the long-term cost savings from increased productivity and reduced rework make it a worthwhile investment.
- Competitive Advantage: Canadian industries that adopt it gain a competitive edge by delivering products faster, with higher quality, and at a competitive price.
In fact, it has found widespread acceptance in Canadian industries.
The automotive, aerospace, and manufacturing sectors have witnessed significant integration of robotic welding systems, reaping the benefits of improved efficiency, quality, and safety.
As robotic technology continues to advance, its adoption in Canadian industries is expected to further increase in the future.
Read: The Environmental Impact of Welding in Canada
Impact on Canadian Manufacturing and Job Market
The impact of robotic welding on the Canadian manufacturing industry
In recent years, robotic welding has made significant advancements in the Canadian manufacturing industry, revolutionizing the way products are made.
This rapid technological transformation has had a profound impact on both production capacity and the job market.
Achieving Increased Production Capacity
- Robotics welding has enabled Canadian manufacturers to achieve higher levels of production capacity.
- Automated systems can work tirelessly, 24/7, without the need for breaks or rest, resulting in increased output.
- With robotic welding, manufacturers can meet growing consumer demands and take on larger orders.
- Increased production capacity has also allowed businesses to expand into new markets and compete globally.
Cost-Effectiveness
- It offers cost-effective solutions for Canadian manufacturers.
- By automating welding processes, companies can significantly reduce labor costs.
- Robots require minimal maintenance and do not require benefits like healthcare or overtime pay.
- Automation reduces the likelihood of costly errors or reworks, resulting in financial savings.
Job Displacement Concerns
- While it brings undeniable benefits, concerns about job displacement have arisen.
- Automation has replaced certain manual welding tasks previously performed by human workers.
- Some argue that robots are a threat to human jobs, leading to unemployment and economic inequality.
- History has shown that technological advancements create new job opportunities and transform industries.
Addressing the Need for Upskilling
- To adapt to technological advancements, Canadian workers in the welding industry need to upskill.
- Upskilling involves acquiring new skills and knowledge to work alongside robotic systems.
- Companies and educational institutions can provide training programs to reskill workers.
- By upskilling, workers can transition to more highly skilled roles, collaborating with robots and overseeing automation.
- Upskilling ensures that the labor force remains valuable and capable of fulfilling new job requirements.
The Role of Collaboration
- To maximize the benefits of robotic welding, collaboration between humans and robots is vital.
- Robots excel in repetitive tasks and heavy lifting, while humans possess problem-solving and critical thinking abilities.
- By working harmoniously, humans and robots can complement each other’s strengths, resulting in improved efficiency.
- Collaboration also opens up opportunities for workers to focus on higher-value tasks that require creativity and innovation.
- Together, humans and robots can drive Canadian manufacturing to new heights.
A Promising Future for Canadian Manufacturing
Robotic welding offers immense potential for the future of Canadian manufacturing.
While some may initially fear job displacement, history has shown that workers can adapt and thrive in a changing economy.
By embracing automation and upskilling, the Canadian workforce can seize new opportunities and drive innovative growth in the manufacturing industry.
In essence, it has had a significant impact on the Canadian manufacturing industry.
Through automation, manufacturers have achieved increased production capacity and cost-effectiveness.
While concerns about job displacement exist, upskilling workers can help them adapt to technological advancements and take on more complex roles alongside robots.
By collaborating with robots, humans can leverage their unique skills and drive Canadian manufacturing towards a promising future.
Read: Safety Standards in Canada’s Construction
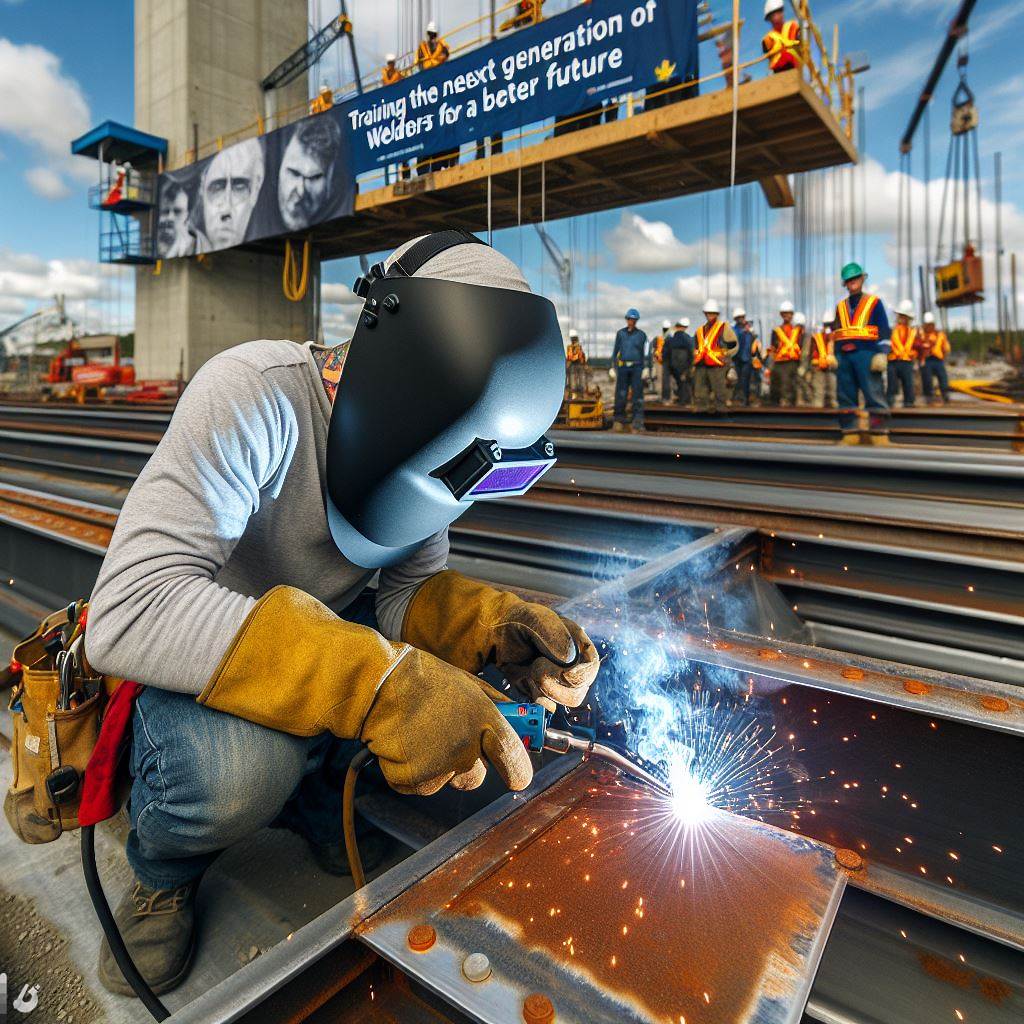
Role of Education and Training
Education and training play a crucial role in supporting the integration of robotic welding technology in Canada’s industrial future.
With the rapid advancements in automation, it is essential to have well-trained individuals who can operate and maintain these sophisticated systems.
Importance of Education and Training Programs
Education and training programs are vital for preparing the workforce to adapt to new technologies and gain the skills required in the field of robotic welding.
These programs provide individuals with the knowledge and expertise needed to work effectively with modern machinery.
By offering specialized courses and certifications, education and training programs help bridge the gap between traditional welding techniques and the latest robotic welding systems.
They ensure that technicians and engineers have a solid foundation in both theoretical concepts and practical skills related to it.
Furthermore, education and training programs create opportunities for individuals to enhance their career prospects and remain competitive in the job market.
As the demand for robotic welding technology increases, employers are actively seeking professionals with relevant qualifications and experience.
Need for Skilled Technicians and Engineers
The integration of this systems requires skilled technicians and engineers who can effectively operate and maintain these sophisticated machines.
Unlike traditional welding methods, it involves working with automated systems that require expert handling.
Skilled technicians play a crucial role in ensuring the optimal performance of robotic welding systems.
They are responsible for programming, monitoring, and troubleshooting the equipment to ensure accurate and efficient welding processes.
Their expertise is invaluable in minimizing downtime and maximizing productivity.
Similarly, engineers with specialized knowledge in robotic welding technology are essential for designing, implementing, and optimizing these systems.
They are involved in the development of robotic welding processes, including programming and integration with other manufacturing processes.
Their role is vital in achieving high-quality welds and ensuring the overall success of automated welding operations.
Initiatives and Institutions Offering Education and Training
Canada has recognized the importance of education and training in supporting the growth of robotic welding technology.
Several initiatives and institutions offer programs and courses that focus on training individuals in this field.
The Canadian Welding Bureau (CWB) is one such initiative that provides welding certification programs, including those specific to robotic welding.
The CWB’s certifications are highly regarded in the industry and ensure that technicians and engineers have the necessary skills and knowledge to meet industry standards.
In addition to the CWB, many colleges and technical institutes across Canada offer specialized programs in robotics and automation.
These programs cover various aspects, including programming, system integration, and maintenance.
Students enrolled in these programs gain hands-on experience with state-of-the-art equipment, preparing them for real-world challenges.
Several industry collaborations and partnerships strive to enhance education and training opportunities.
These collaborations often involve manufacturers, educational institutions, and government bodies working together to develop curriculum frameworks, provide funding, and promote research in the field.
This collective effort aims to produce a workforce that is well-equipped to handle the demands of robotic welding technology.
In general, education and training programs are crucial in supporting the integration of robotic welding technology in Canada’s industrial future.
They provide individuals with the necessary knowledge and skills, contribute to the availability of skilled technicians and engineers, and are backed by initiatives and institutions that prioritize the advancement of this field.
Read: Electrician Salary Ranges in Canada’s Provinces
Government Initiatives and Support
Government initiatives aimed at promoting the adoption of robotic welding technology in Canada
In this context, Government initiatives play a crucial role in promoting the adoption of robotic welding technology in Canada.
These initiatives aim to drive innovation, competitiveness, and economic growth in the industrial sector.
Funding Opportunities
The Canadian government provides various funding opportunities to support the implementation and advancement of robotic welding technology.
These funding programs enable businesses to invest in equipment, research, and employee training.
- The Strategic Innovation Fund (SIF) offers financial support to businesses engaged in innovative and collaborative projects. It encourages partnerships between industry, academia, and research institutions to accelerate the adoption of new technologies like robotic welding.
- The Canada Foundation for Innovation (CFI) provides research grants to support infrastructure development in universities and colleges. This funding assists in creating cutting-edge research facilities for advancements in robotic welding technology.
- The Industrial Research Assistance Program (IRAP) offers financial support and technical expertise to Canadian small and medium-sized enterprises (SMEs) for development and commercialization of innovative technologies. Eligible businesses can receive funding to adopt and integrate robotic welding systems into their operations, enhancing their competitiveness.
Research Grants
The Canadian government also supports research and development initiatives focused on robotic welding technology.
Research grants help fuel innovation and push the boundaries of what is possible in this field.
- The Natural Sciences and Engineering Research Council of Canada (NSERC) provides grants to academic and industry researchers investigating new techniques, materials, and applications in robotic welding. This research contributes to the development of more efficient and reliable welding processes.
- The Mitacs program facilitates collaborative research between academia and industry. Through Mitacs grants, researchers can partner with businesses to develop and optimize robotic welding technologies. This partnership enhances knowledge transfer and promotes the practical application of research outcomes.
- Colleges and institutes across Canada also offer research grants to faculty and students engaged in robotics research. These grants support projects exploring advancements in robotic welding, including programming, sensor integration, and process optimization.
Partnerships with Industry Stakeholders
The Canadian government recognizes the importance of collaboration between industry stakeholders to drive the adoption and success of robotic welding technology.
- The National Research Council of Canada Industrial Research Assistance Program (NRC-IRAP) provides financial support and technical advice to businesses for technology adoption. By partnering with NRC-IRAP, companies can access expertise and resources to implement robotic welding systems and boost their competitiveness.
- The Canadian Welding Association (CWA) collaborates with government agencies, educational institutions, and industry partners to promote the use of robotic welding. Through training programs, certifications, and industry events, CWA supports the development of a skilled workforce and the widespread adoption of robotic welding technology.
- The CenterLine (Windsor) Limited Innovation Centre partners with educational institutions and research organizations to advance robotic welding technologies. This collaboration fosters the exchange of knowledge, promotes best practices, and drives continuous improvement in the field of robotic welding.
In brief, the Canadian government demonstrates its commitment to advancing robotic welding technology through various initiatives.
By providing funding opportunities, research grants, and fostering partnerships, the government plays a vital role in driving innovation and supporting it adoption in Canada’s industrial future.
See Related Content: Safety Protocols for Electricians in Canada
Challenges and Future Outlook
Robotic welding technology has revolutionized the industrial landscape in Canada, offering increased efficiency, precision, and safety.
As with any technology, there are potential challenges and limitations that need to be addressed to further advance the field.
Potential Challenges
- Programming Complexity: One of the challenges with robotic welding is the complexity of programming the robots. It requires skilled technicians who can understand welding techniques and translate them into robot code.
- Adapting to Variations: The ability of robotic welding systems to adapt to variations in workpieces and welding conditions can be limited. This poses challenges when dealing with complex or irregularly shaped components.
- Welding of Dissimilar Materials: Robotic welding technology may face challenges when it comes to welding dissimilar materials, such as joining aluminum and steel. Achieving strong and reliable welds between different materials can be difficult.
- Human Supervision: While robotic welding systems are designed to operate autonomously, human supervision is still required to ensure proper functioning, maintenance, and quality control. This reliance on human oversight suggests a limit to fully autonomous robotic welding.
Ongoing Research and Development Efforts
Despite the challenges, ongoing research and development efforts are being made to overcome these limitations and further advance robotic welding technology in Canada.
- Advanced Sensing and Vision Systems: Research is being conducted to enhance the capabilities of robotic welders in sensing and vision systems. This would enable robots to better adapt to variations in workpieces, improving weld quality and accuracy.
- Intelligent Software and Path Planning: Developments in intelligent software and path planning algorithms are underway to simplify the programming complexity of robotic welders. This would make them more accessible to a wider range of technicians.
- Material and Process Innovation: Research is focused on improving the welding process itself, exploring new methods and technologies for welding dissimilar materials. This could open up new possibilities for joining different metals in various industries.
- Collaborative Robots: Collaborative robots, also known as cobots, are being developed and integrated into the welding process. These robots can safely work alongside human operators, combining the expertise of both to achieve superior results.
Positive Outlook on the Future of Robotic Welding in Canada
The future of robotic welding in Canada looks promising, despite the challenges and limitations.
The advancements in technology and ongoing research efforts suggest a positive outlook.
- Economic Prosperity: Robotic welding has the potential to contribute significantly to Canada’s economic prosperity. Increased efficiency and productivity achieved through automation can reduce costs and improve competitiveness in various industries.
- Skilled Workforce Development: The adoption of robotic welding technology requires skilled technicians who can program, operate, and maintain these systems. This can lead to the development of a highly skilled workforce, enhancing Canada’s industrial capabilities.
- Improved Safety and Working Conditions: Robotic welding systems can improve working conditions for welders by minimizing exposure to hazardous fumes, intense heat, and physical strain. This promotes a safer and healthier work environment.
- Increased Quality and Consistency: With precise control and repeatability, robotic welding can ensure consistent quality and reduce defects. This leads to improved product reliability, customer satisfaction, and overall competitiveness.
In a nutshell, while robotic welding technology in Canada faces certain challenges and limitations, ongoing research and development efforts are actively addressing these issues.
The potential for growth and economic prosperity, along with improved safety and quality, makes the future of robotic welding in Canada bright.
Conclusion
Robotic welding technology holds immense potential for Canada’s industrial future.
Embracing this technology is crucial for securing the country’s manufacturing sector.
The key points discussed in this blog post include the efficiency and precision of robotic welding, the ability to increase production rates, and the cost-effectiveness it provides.
TFurthermore, the role of automation and innovation in driving forward the Canadian manufacturing sector cannot be underestimated.
By integrating robotic welding technology, businesses can stay competitive, ensure quality, and meet the demands of a rapidly evolving industry.
As Canadian manufacturers face increased global competition, it is essential to embrace advancements like robotic welding to maintain a strong foothold in the international market.
The future success of Canada’s manufacturing sector relies on leveraging innovative technologies to enhance productivity and optimize efficiency.
It is imperative that companies invest in robotic welding technologies to secure their place in the country’s industrial future.
By embracing automation and implementing cutting-edge solutions, Canadian manufacturers can position themselves as leaders in the global market, fostering sustainable growth and economic prosperity.