Introduction
In this blog post, we will explore the concept of mobile welding and its significance in the industry.
Mobile welding refers to the practice of performing welding tasks in various locations, as opposed to a traditional static welding shop.
It has gained immense importance in the industry due to its versatility and convenience.
This blog post aims to shed light on the benefits and challenges of mobile welding.
Additionally, it will discuss the equipment and skills required for successful mobile welding.
The purpose of this post is to educate readers about this emerging trend and provide insights for both aspiring mobile welders and potential clients.
Through this section, we hope to inspire individuals to explore the opportunities that mobile welding presents and encourage innovation in the welding industry.
With mobile welding, the possibilities are endless, and it is time to embrace this new era in welding.
Advantages of Mobile Welding
The advantages of mobile welding in the industry are numerous and beneficial for both clients and welders.
Increased accessibility
The increased accessibility provided by mobile welding services brings welding expertise directly to the client’s location, regardless of how remote or inaccessible it may be.
This accessibility is especially advantageous for clients who have heavy equipment or structures that cannot easily be transported to welding shops.
Cost-effectiveness
Additionally, mobile welding is highly cost-effective.
It eliminates the need for transportation, thereby reducing costs associated with moving items to a welding facility.
Clients no longer have to spend on dismantling or disassembling large structures, saving both time and money.
The ability to work on-site also reduces labor costs, as there is no need to hire extra workers for transportation purposes.
Time-saving
Another significant advantage of mobile welding is its time-saving nature.
Clients can benefit from on-site welding services, avoiding the time-consuming process of transporting items.
Mobile welders are readily available, eliminating waiting times often associated with traditional welding services.
There is no downtime caused by transportation or waiting for projects to be completed off-site.
Flexibility
Flexibility is another key advantage of mobile welding. Mobile welders offer services at any location, adapting to the client’s schedule.
This flexibility allows clients to schedule welding services at their convenience, minimizing disruptions to their operations.
Mobile welders are versatile and can work on various projects, whether it’s repairs, maintenance, or even custom fabrication.
In short, mobile welding has revolutionized the industry by providing increased accessibility, cost-effectiveness, time-saving benefits, and flexibility.
Clients can now easily access welding services regardless of their location, saving time and money in the process.
The on-site nature of mobile welding enhances flexibility and allows for a seamless integration into clients’ schedules.
Unlock Your Career Potential
Visualize a clear path to success with our tailored Career Consulting service. Personalized insights in just 1-3 days.
Get StartedWith these advantages, mobile welding has truly ushered in a new era in the welding industry.
Read: Welding Apprenticeships: What to Expect
Applications of Mobile Welding
Construction
Mobile welding in the construction industry has revolutionized the way projects are executed.
With the ability to bring welding services directly to construction sites, it offers great convenience and efficiency.
Construction companies no longer need to transport heavy materials to off-site welding workshops, reducing both time and costs.
Additionally, mobile welding provides the flexibility to weld in various positions and angles, ensuring precise and accurate constructions.
Infrastructure Repair
Mobile welding plays a crucial role in the repair of infrastructure, such as bridges and pipelines.
Rather than removing the damaged sections entirely, mobile welders can be dispatched to the repair site, saving a significant amount of time and resources.
These skilled professionals can efficiently repair and reinforce structures, ensuring their longevity and safety.
Mobile welding allows for quick response during emergencies, preventing further damage and minimizing disruptions.
Automotive Industry
Mobile welding has revolutionized the automotive industry by providing on-demand welding services.
Whether it’s repairing a damaged chassis, fixing exhaust systems, or reinforcing frames, mobile welders offer a convenient solution.
Automakers and repair shops can now easily access welding professionals without transporting vehicles to traditional welding facilities.
This expedites the repair process, reducing downtime and increasing overall productivity in the industry.
Manufacturing Sector
The manufacturing sector greatly benefits from it due to its flexibility and convenience.
Mobile welders can provide on-site welding services during the production processes, minimizing downtime caused by transporting components to welding facilities.
This ensures a smooth and continuous manufacturing workflow, resulting in increased efficiency and reduced costs.
Moreover, it enables manufacturers to maintain quality control throughout the production cycle, as immediate repairs can be made.
It has transformed various industries, including construction, infrastructure repair, automotive, and manufacturing.
Its ability to provide on-site welding services has improved efficiency, reduced costs, and minimized disruptions.
As technology advances, it is expected to further revolutionize the industry.
With the increasing demand for immediate welding services, mobile welders will continue to play a crucial role in ensuring the seamless execution of projects.
Read: How to Start Your Welding Career in Canada
Challenges and Considerations in Mobile Welding
In mobile welding, welders encounter several challenges and considerations that differ from traditional welding in a dedicated workshop.
These factors can significantly impact the workflow and overall success of a project in this context.
Being aware of these challenges and taking the necessary precautions is crucial to ensure safety, quality, and efficiency.
Limited workspace
One of the primary challenges is the limited workspace.
Welders often find themselves working in tight and confined areas, such as construction sites or repairs in small buildings.
This restricted space can make it difficult for welders to maneuver and access different welding angles.
To overcome this challenge, welders need to adapt to space constraints and find innovative solutions to complete their work effectively.
Safety precautions
Safety precautions play a vital role in context.
The nature of mobile welding, being performed in various work environments, calls for a strict adherence to safety measures.
Welders must always wear proper protective equipment, including helmets, gloves, and fire-resistant clothing.
Regular inspections of equipment and ensuring a safe working environment are essential to prevent accidents and injuries.
Equipment portability
Equipment portability is another consideration in context.
Welders need to invest in lightweight and durable welding machines that can withstand frequent moves.
Portable welding equipment allows welders to bring their tools to different job sites efficiently.
Ensuring the right balance between weight, size, and durability is crucial to optimize mobility and ease of use.
Weather conditions
Weather conditions pose a significant challenge for mobile welders.
Unlike traditional welding indoors, mobile welding is often performed outdoors, exposing welders to the elements.
Rain, wind, and extreme temperatures can affect the quality and integrity of welds if not properly accounted for.
Welders must have adequate shelter, such as a portable canopy, to protect the welding area from weather conditions.
Taking precautionary measures and planning around the weather can ensure successful projects.
In general, mobile welding presents unique challenges and considerations compared to welding in traditional workshops.
Limited workspace requires adaptation and creativity, while safety precautions must be strictly adhered to ensure personal well-being.
Equipment portability plays a crucial role in optimizing mobility and efficiency. Lastly, weather conditions should be carefully considered to protect the integrity of welds.
By understanding and addressing these challenges, mobile welders can thrive in this new era of the industry.
Read: Salary Guide: Welders in Canada 2024
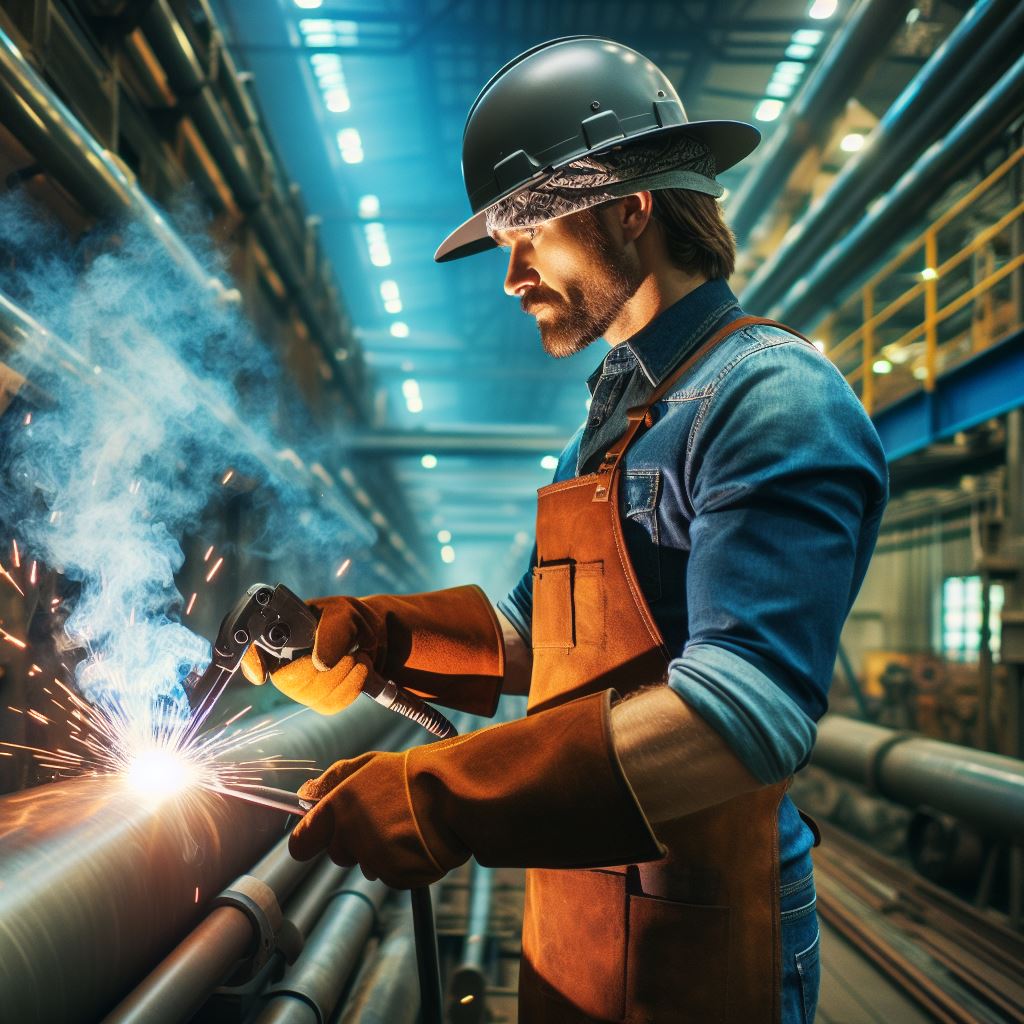
Skills and Qualifications Required for Mobile Welding
- Welding certifications are essential for mobile welders to demonstrate their expertise and qualifications.
- A mobile welder should possess a strong knowledge of various techniques, such as MIG, TIG, and so on.
- Problem-solving abilities are crucial for mobile welders to overcome any challenges or obstacles they may encounter on the job.
- Effective communication skills are necessary for mobile welders to interact with clients, understand project requirements, and provide updates.
A mobile welder’s success and efficiency depend on the mastery of different skills and qualifications.
Let’s take a closer look at each of the essential aspects for mobile welding:
Welding certifications
These welders must have various welding certifications to validate their expertise and ensure their work meets industry standards:
- Common certifications include Certified Welder (CW), Certified Welding Inspector (CWI), and Certified Welding Educator (CWE).
- These certifications validate a welder’s ability to produce quality welds and comply with safety regulations.
- Additionally, certifications demonstrate a welder’s knowledge of different welding processes, materials, and codes.
Knowledge of different welding techniques
Mobile welders should have a comprehensive understanding of various welding techniques to adapt to different project needs:
- MIG (Metal Inert Gas) welding is commonly used for joining thick materials and offers high productivity.
- TIG (Tungsten Inert Gas) welding is suitable for precise and intricate welds on thin materials.
- Stick welding, or Shielded Metal Arc Welding (SMAW), is a versatile method that works well in outdoor environments.
Problem-solving abilities
Mobile welders often face unexpected challenges on-site and must possess strong problem-solving skills to overcome them:
- They need to quickly assess and troubleshoot issues such as equipment malfunctions or structural limitations.
- Adaptability is essential as each welding project may present unique obstacles that require creative solutions.
- Mobile welders should possess a strong attention to detail and the ability to find innovative approaches to ensure project success.
Communication skills
Effective communication is vital for mobile welders as they interact with clients, contractors, and other team members:
- They should be able to clearly understand project requirements and client expectations.
- Excellent listening skills allow welders to comprehend specific needs and deliver accurate results.
- Regular communication and updates help maintain transparency and ensure all parties are on the same page.
In a nutshell, mobile welding requires a combination of essential skills and qualifications to excel in the industry.
Welding certifications, knowledge of different techniques, problem-solving abilities, and communication skills are crucial for mobile welders to provide high-quality and efficient services.
Developing and honing these skills is vital for individuals aiming to thrive in the mobile field.
Read: Pros and Cons of a Welding Career in Canada
Future Trends in Mobile Welding
Technological advancements
With the rapid advancements in technology, mobile welding is expected to witness significant improvements in the future.
These advancements will revolutionize the industry, making it faster, more efficient, and safer.
- Portable welding equipment: The development of compact and lightweight welding machines will enable welders to easily transport their equipment to any location, eliminating the need for heavy and bulky machinery.
- Specialized mobile apps: The rise of mobile apps tailored for welders will provide valuable resources, such as welding specifications, welding technique tutorials, and project management tools, enhancing productivity on the go.
- Advanced welding techniques: Innovative welding techniques, such as friction stir welding and laser welding, will become more prevalent. These techniques offer higher precision and quality, leading to stronger and more durable welds.
Automation and robotics in mobile welding
The integration of automation and robotics in mobile welding processes is a game-changer for the industry.
These advancements will bring efficiency, accuracy, and cost-effectiveness to welding operations.
- Robotic welders: Mobile welding robots equipped with artificial intelligence capabilities will be able to perform intricate welds with unmatched precision and speed. This automation will eliminate human errors and reduce the risk of accidents.
- Collaborative robots: Collaborative robots, also known as cobots, will work alongside human welders, enhancing their productivity by handling repetitive tasks and lifting heavy objects, while the welder focuses on more complex welds.
- Remote welding operations: Remote-controlled robotic welding systems will enable welders to perform tasks in hazardous or hard-to-reach areas without physical presence. This technology increases safety and saves time by eliminating the need for human entry into dangerous environments.
Integration of augmented reality
Augmented reality (AR) is set to revolutionize mobile welding, offering welders advanced tools for visualizing, planning, and executing welds.
- AR welding helmets and goggles: Welders will have access to AR-enabled welding helmets and goggles that overlay important welding parameters, such as heat input and weld dimensions, onto the welder’s field of view in real-time.
- Remote assistance: AR technology will allow experienced welders to provide real-time guidance and assistance to less experienced welders through remote augmented reality sessions. This collaboration enhances skill development and problem-solving on the job.
- Weld path visualization: AR systems will project the intended weld path onto the workpiece before the actual welding process begins. This visualization eliminates guesswork, ensures accurate weld placement, and reduces errors.
In summary, the future of mobile welding looks promising with the integration of technological advancements, automation, robotics, and augmented reality.
These trends will enhance productivity, quality, and safety in the industry, making it a crucial component of the evolving welding sector.
Conclusion
Mobile welding offers numerous benefits, including convenience, flexibility, and cost-effectiveness.
It transforms industries with flexibility, cost-effectiveness, and rapid response capabilities. On-site solutions elevate project efficiency.
The industry has great potential for growth, fueled by the increasing demand for mobile welding services.
The industry’s potential growth is immense, driven by increasing demand for on-the-go welding services. Adaptability fosters sustainability and innovation.
Explore lucrative opportunities. Embrace the freedom to weld anywhere, unlocking a dynamic career path. Your journey awaits!
Readers are encouraged to explore the opportunities in mobile welding to tap into this expanding market.