Overview of Metal Fabrication
Definition
Metal fabrication involves creating metal structures through cutting, bending, and assembling processes.
This discipline is crucial for various industries, including construction, automotive, and aerospace.
Fabricators work with different metals, such as steel, aluminum, and copper.
Importance of Metal Fabrication
Metal fabrication plays a vital role in manufacturing durable products.
It allows engineers to design custom solutions tailored to specific needs.
Additionally, it supports the development of innovative technologies and applications.
This field contributes significantly to both local and global economies.
Moreover, metal fabrication enhances product efficiency and performance.
Applications of Metal Fabrication
Metal fabrication is present in many sectors, including construction and machinery.
It is essential for creating frameworks, platforms, and other structural components.
Moreover, it is involved in the production of machinery parts and tools.
Aerospace relies on metal fabrication for structural components of aircraft and satellites.
Skills and Expertise Required
Professional metal fabricators require a solid understanding of metallurgy.
They must also possess skills in welding, cutting, and machining.
Attention to detail is crucial for achieving high-quality outcomes.
Furthermore, proficiency in reading blueprints and technical drawings is essential.
Safety Gear and Equipment Used in Metal Fabrication
Importance of Safety Gear
Safety gear is crucial in metal fabrication environments.
It protects workers from potential hazards and injuries.
Using the right equipment enhances overall safety.
You must prioritize safety to maintain a productive workspace.
Types of Safety Gear
Various types of safety gear are essential for metal fabricators.
Some common items include gloves, helmets, and safety goggles.
- Gloves protect hands from sharp edges and burns.
- Helmets shield heads from falling objects.
- Safety goggles guard against flying debris.
Additionally, ear protection is necessary in loud environments.
Respirators may be required when working with harmful fumes.
Working with Equipment
Metal fabricators utilize various tools and machines.
Unlock Your Career Potential
Visualize a clear path to success with our tailored Career Consulting service. Personalized insights in just 1-3 days.
Get StartedUsing safety equipment reduces the risk of accidents.
Wearing the appropriate gear ensures compliance with safety regulations.
Training staff on equipment use is equally important.
Regular inspections of safety gear can prevent malfunctions.
Maintenance of Safety Gear
Proper maintenance of safety gear is vital for effectiveness.
Regular cleaning extends the lifespan of equipment.
Inspecting gear for wear and tear is essential.
Promptly replace damaged items to maintain protection levels.
Involving staff in maintenance routines enhances safety culture.
Cutting Tools: Types and Applications in Metal Fabrication
Overview of Cutting Tools
Cutting tools are essential for metal fabrication processes.
These tools utilize various methods to cut metal accurately.
Understanding the types of cutting tools helps fabricators choose the right one for specific tasks.
Types of Cutting Tools
Laser Cutters
Laser cutters use focused laser beams to cut through metal efficiently.
They produce high-quality cuts with minimal kerf loss.
Additionally, laser cutters are suitable for intricate designs.
Plasma Cutters
Plasma cutters employ hot plasma to sever metal sheets.
These tools work well on thick materials and are highly portable.
Moreover, plasma cutters offer speed and versatility in various applications.
Oxy-Fuel Cutters
Oxy-fuel cutting involves a flame generated by burning acetylene and oxygen.
This method is effective for cutting and welding steel and other ferrous metals.
It is particularly useful for thicker materials.
Band Saws
Band saws utilize a long blade with teeth to perform straight cuts.
These tools are perfect for precise cuts on various metals.
Moreover, band saws can handle different thicknesses effectively.
Applications of Cutting Tools
Cutting tools have numerous applications in the metal fabrication industry.
They are crucial in manufacturing parts for automotive and aerospace industries.
Moreover, they play a vital role in structural steel work.
Additionally, cutting tools assist in creating prototypes for product development.
Choosing the Right Cutting Tool
Selecting the appropriate cutting tool depends on several factors.
Consider the type and thickness of the metal you will cut.
Furthermore, evaluate the desired precision and finish quality.
Lastly, think about the available budget and operational costs.
Explore Further: Challenges and Rewards of Residential Roofing Jobs
Joining Techniques: Welding and Soldering Tools
Welding Overview
Welding is a fundamental metal joining technique in fabrication.
This method uses high heat to melt materials and bond them together.
Welders often forgo fillers for stronger joints in many applications.
Types of Welding Processes
There are several welding processes professionals utilize.
- MIG welding is popular for its versatility and ease of use.
- TIG welding provides precise control for thin materials.
- Stick welding is valued for its simplicity and durability.
Essential Welding Equipment
Professionals require specific tools for effective welding.
- A welding machine generates the necessary heat.
- Protective gear ensures safety during the welding process.
- Welding rods or wires facilitate the joining of metal.
Soldering Overview
Soldering is another technique essential in metal fabrication.
This method joins materials using a filler metal that melts at a lower temperature.
It often finds use in electronics and intricate designs.
Key Soldering Materials
Essential materials enhance soldering effectiveness.
- Solder alloys blend various metals for desired properties.
- Flux helps clean surfaces and improve metal bonding.
- Soldering irons provide the necessary heat application.
Applications of Soldering
Soldering is crucial for connecting electronic components.
This technique allows for repairs and modifications in circuits.
Moreover, it is useful in jewelry making and plumbing tasks.
Delve into the Subject: How Upholsterers Collaborate with Designers and Architects
Bending and Forming Equipment: Press Brakes and Rollers
Overview of Bending and Forming
Bending and forming are crucial processes in metal fabrication.
They shape materials into desired angles and profiles.
Different machines assist with these processes effectively.
Press Brakes
Press brakes are essential for bending sheet metal.
They use a punch and die to create precise bends.
Operators can customize bends according to project requirements.
Modern press brakes feature advanced controls for accuracy.
This technology allows for repeatable and intricate designs.
Types of Press Brakes
There are several types of press brakes available.
- Mechanical Press Brakes harness mechanical systems.
- Hydraulic Press Brakes use hydraulic force for more power.
- Electric Press Brakes offer energy-efficient solutions.
Rollers
Rollers are used to create curves in metal sheets.
They can form cylindrical shapes or arcs with precision.
This equipment usually consists of three rollers.
The configuration of rollers determines the material thickness.
Types of Rollers
Different types of rollers cater to various needs.
- Slip Rollers are suitable for thin materials.
- Plate Rolls work effectively with thicker materials.
- Section Benders can create complex shapes and profiles.
Importance of Proper Equipment
Using the right equipment enhances production efficiency.
It leads to better quality and reduces waste in fabrication.
Investing in modern bending and forming tools is essential.
This investment pays off through improved craftsmanship.
Learn More: Upholsterers and the Growing Demand for Custom Work
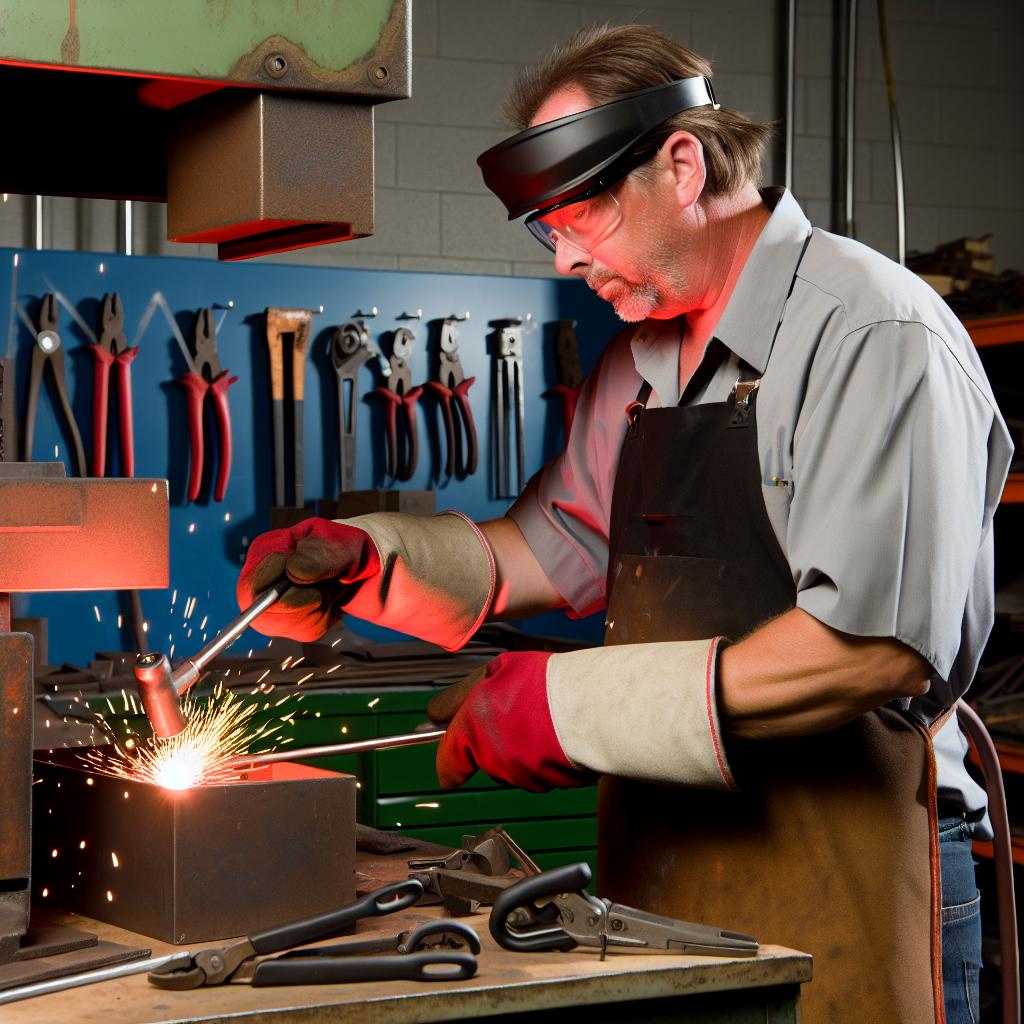
Finishing Tools: Grinders, Sanders, and Polishers
Introduction to Finishing Tools
Finishing tools are essential in metal fabrication.
They provide smooth surfaces, ensuring quality and aesthetics.
Moreover, they can remove imperfections from metalwork.
Grinders: Versatile Powerhouses
Grinders come in various types for different applications.
Angle grinders are ideal for cutting and grinding materials.
Bench grinders are excellent for sharpening tools.
Additionally, die grinders are perfect for precision work.
Each type offers unique advantages for metal fabricators.
Common Uses of Grinders
- Removing excess material from welds.
- Sharpening cutting tools and bits.
- Preparing surfaces for painting or coating.
Sanders: Achieving a Smooth Finish
Sanders play a vital role in achieving smooth finishes on metal surfaces.
Orbital sanders provide a swirl-free finish, making them popular.
Moreover, belt sanders work effectively for heavy material removal.
Each type of sander offers unique benefits based on the project.
Applications of Sanders
- Finishing surfaces before welding or coating.
- Removing rust and old paint from metal surfaces.
- Smoothing out rough edges on fabricated parts.
Polishers: For a Mirror-Like Shine
Polishers add the final touch to metal projects.
They can create high-gloss finishes, enhancing appearance.
Additionally, they help protect metals from corrosion.
Different types of polishers cater to various materials.
Key Benefits of Using Polishers
- Enhancing the aesthetic appeal of finished products.
- Providing a protective layer against environmental elements.
- Improving the durability of metal surfaces.
Maintaining Finishing Tools
Proper maintenance ensures the longevity of finishing tools.
Regular cleaning helps prevent material buildup.
Furthermore, checking for wear and tear is critical.
Following manufacturer guidelines enhances performance.
Explore Further: Key Business Tips for Aspiring Upholstery Professionals
Measuring and Layout Tools
Importance of Precision
Precision is crucial in metal fabrication.
Accurate measurements ensure quality finished products.
This reduces waste and saves time and resources.
Common Measuring Tools
Fabricators commonly use calipers for precise measurements.
These tools measure internal and external dimensions accurately.
Tape measures are also popular for larger sections.
They provide a quick way to gauge length and width.
Laser distance measurers offer advanced accuracy.
They eliminate errors caused by parallax with traditional methods.
Layout Tools for Metal Fabrication
Layout tools define where cuts and bends occur.
Chalk lines create straight reference lines on large panels.
These lines help ensure cuts follow intended paths.
Squares and bevel gauges aid in maintaining right angles.
A protractor is essential for measuring and marking angles.
Techniques for Effective Measurement
Always calibrate tools before taking measurements.
Use consistent units of measurement throughout the project.
Double-check measurements to catch potential errors.
Document measurements for improved accuracy and clarity.
Emerging Technologies: CNC Machines and Automation in Metal Fabrication
Introduction to CNC Machines
CNC machines revolutionize metal fabrication processes.
They automate tasks which traditionally required manual intervention.
This technology increases precision and efficiency in manufacturing.
Benefits of CNC Machines
CNC machines offer numerous advantages over manual processes.
They significantly reduce human error in fabricating components.
Moreover, they enhance repeatability in production runs.
Additionally, CNC machines can operate continuously, increasing output.
Exploring Automation in Metal Fabrication
Automation streamlines various operations within metal fabrication.
It allows manufacturers to optimize workflows effectively.
This process integrates various technologies, including robotics and AI.
Robotic systems handle repetitive tasks, improving worker safety.
The Role of Robotics
Robots play a crucial role in modern fabrication facilities.
They execute precise welding, cutting, and assembling tasks.
Consequently, the use of robots minimizes physical strain on workers.
Automation can also lead to reduced operational costs in the long run.
Innovative Software Solutions
Software tools enhance the functionality of CNC machines.
They enable manufacturers to design and simulate projects digitally.
This process improves planning and reduces material waste.
Furthermore, advanced software allows real-time monitoring of production.
Impacts on Workforce and Training
The rise of CNC machines and automation changes workforce requirements.
Employees need new skills to operate advanced equipment.
Training programs now emphasize technological proficiency.
This shift ensures workers remain valuable in an evolving industry.
Additional Resources
Best pro-level automotive tool brand other than Snap On/Matco etc …