Introduction
“Embarking on a nuanced exploration of ‘Canadian Welding Standards: An Overview’ reveals a multifaceted tapestry that goes beyond mere regulatory frameworks.
These standards serve as the backbone of an industry that demands precision, safety, and adaptability.
Delving deeper, we uncover the meticulous scrutiny applied to structural integrity, the discerning eye cast upon material compatibility, and the intricate dance between innovation and tradition.
This comprehensive overview not only dissects the technical intricacies of welding but also underscores the role these standards play in fostering a culture of excellence.
They are not just guidelines but a testament to a commitment to craftsmanship, ensuring that each weld stands as a testament to both the artistry and engineering acumen of professionals in the field.
As we navigate this intricate web, we unravel not only the regulatory landscape but also the stories of resilience, innovation, and collaboration that characterize the Canadian welding industry.
Join us on this illuminating journey as we peer into the welder’s world, where precision meets passion, and standards become the keystones of a resilient and thriving welding community.
Canadian Welding Standards
Definition and Purpose of Welding Standards
Welding standards are guidelines that provide industry best practices, safety requirements, and quality criteria for welding processes.
Explanation of the Canadian Welding Bureau (CWB)
The CWB is a non-profit organization responsible for the development and maintenance of welding standards in Canada.
Overview of the Standards Set by the CWB
The CWB sets several standards that cover different aspects of welding in various industries.
CSA W59 – Welded Steel Construction
CSA W59 standard provides guidelines for welding steel used in the construction industry.
It covers structural welding requirements and inspection criteria.
CSA W47.1 – Fusion Welding of Steel
In this context, CSA W47.1 is the standard for fusion welding of steel, including requirements for welding procedures, qualification of welders, and inspection of welded joints.
CSA W48 – Filler Metals and Allied Materials for Metal Arc Welding
The CSA W48 standard focuses on the classification and selection of filler metals and allied materials used in metal arc welding processes.
CSA W59.2 – Welded Aluminum Construction
The CSA W59.2 provides guidelines specifically for welding aluminum used in structural applications, ensuring the strength and integrity of welded aluminum structures.
These standards play a crucial role in ensuring the safety, reliability, and quality of welded products in Canada.
They help minimize the risk of weld failures, ensure consistency in welding processes, and foster industry-wide best practices.
Adhering to these standards not only enhances the overall performance of welded products but also promotes a high level of confidence among customers, as the standards ensure that the products meet stringent quality and safety requirements.
The CWB, in collaboration with industry experts, continuously updates and revises these standards to keep pace with technological advancements and changing industry needs.
This ongoing effort ensures that Canadian welding standards remain up-to-date and aligned with international best practices.
In short, welding standards set by the Canadian Welding Bureau (CWB) serve as guidelines for various welding processes, materials, and constructions.
These standards, such as CSA W59, CSA W47.1, CSA W48, and CSA W59.2, ensure the safety, quality, and reliability of welded products in Canada.
By adhering to these standards, the welding industry can deliver superior products while maintaining customer trust and satisfaction.
Read: Welding Safety 101: Essential Tips and Gear
Importance of Adhering to Welding Standards
Adhering to welding standards is crucial for several reasons:
Unlock Your Career Potential
Visualize a clear path to success with our tailored Career Consulting service. Personalized insights in just 1-3 days.
Get StartedEnsuring safety and quality in welding practices
- Following welding standards helps to minimize the risk of accidents and injuries.
- Adhering to the standards ensures that proper safety measures are implemented during welding operations.
- It helps to guarantee the structural integrity and performance of welded products.
- Standardized practices contribute to the production of high-quality welds, which leads to customer satisfaction.
Meeting legal and regulatory requirements
- Adhering to welding standards allows companies to comply with specific laws and regulations related to welding.
- Failure to meet these requirements can result in legal liabilities and financial penalties.
- Meeting the necessary standards also ensures a seamless certification process for welding professionals.
- It helps companies avoid legal disputes and maintain a positive reputation in the industry.
Ensuring compatibility and reliability of welded structures and components
- Welding standards provide guidelines for selecting appropriate welding techniques and materials.
- By adhering to these standards, welding professionals can ensure compatibility between different welded components.
- Following the recommended procedures and specifications ensures the long-term reliability of welded structures.
- It helps prevent failures, cracks, or other defects that could compromise the integrity of the welds.
Enhancing international competitiveness in the welding industry
- Adhering to welding standards allows Canadian welding companies to compete on a global scale.
- Complying with international standards improves the acceptance and marketability of Canadian welds abroad.
- It facilitates international trade by ensuring that Canadian welding products meet the required standards of other countries.
- Following recognized guidelines and standards enhances the reputation of Canadian welders and companies worldwide.
In fact, adhering to welding standards is of utmost importance for ensuring safety, maintaining quality, meeting legal requirements, and enhancing international competitiveness in the welding industry.
By following these standards, welders can not only safeguard themselves and others but also produce reliable and high-quality welded structures and components.
Read: Women in Welding: Changing the Industry
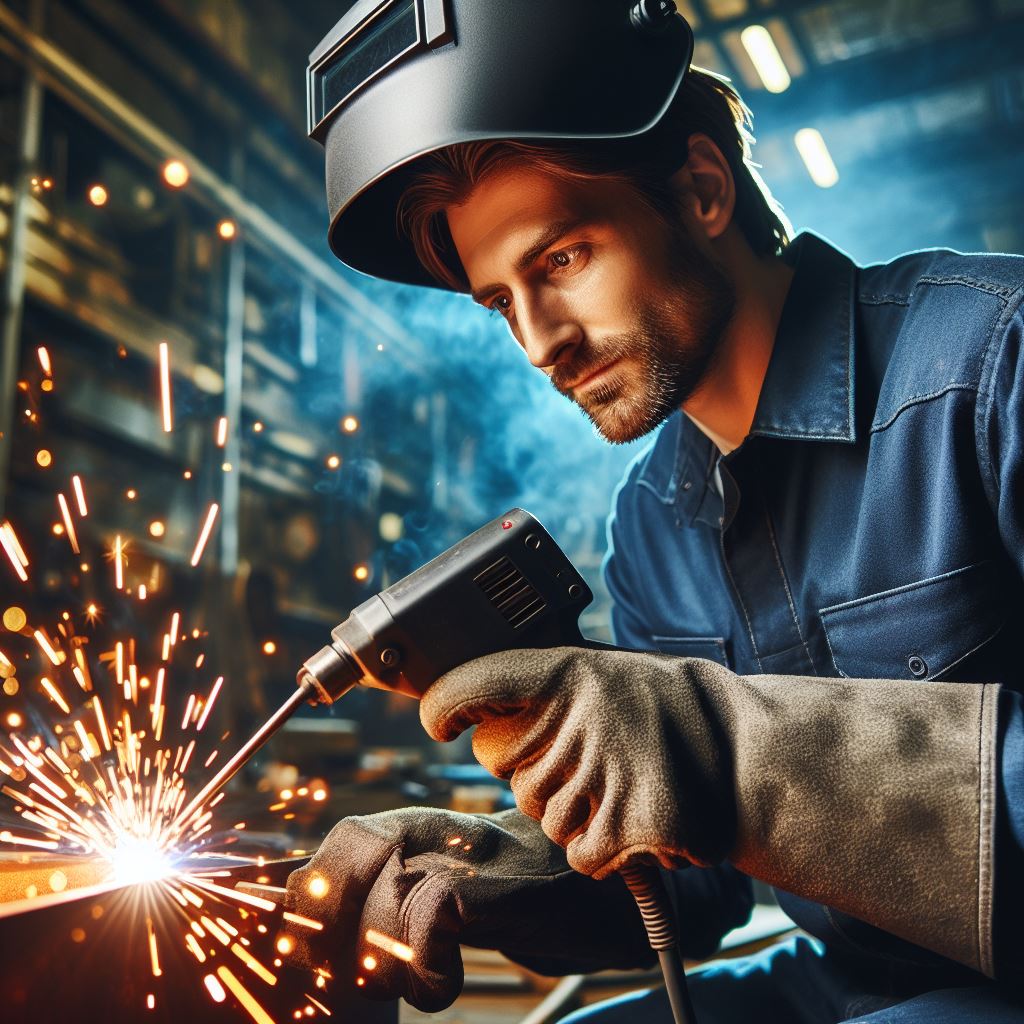
Certification and Training Process
Overview of the certification process by the CWB
- The CWB follows a rigorous certification process for welders to ensure their competence.
- Applicants must meet specific criteria and pass a series of tests to obtain certification.
- The process involves a combination of written exams, practical assessments, and performance evaluations.
- Successful candidates are granted certification that is recognized and respected in the industry.
Explanation of the various certification levels
- The CWB offers different levels of certification based on the welder’s skills and experience.
- Entry-level certification is aimed at beginners who have limited welding experience.
- Intermediate and advanced levels require more training, experience, and the ability to handle complex welding tasks.
- Each certification level has specific requirements that welders must fulfill to progress further.
Importance of proper training and qualification for welders
- Proper training and qualification are crucial for welders to ensure their safety and the quality of their work.
- Qualified welders have a better understanding of welding techniques, safety procedures, and equipment operation.
- They are also more adept at identifying potential welding defects and taking corrective measures.
- Clients and employers prefer certified welders as they demonstrate competence and commitment to their profession.
Introduction to the Welding Education, Training and Certification Program (WETC)
- The WETC is a comprehensive program that aims to provide standardized welding training and certification.
- It is designed to meet industry demands and ensure consistency in the skills and knowledge of welders.
- The program covers various welding processes, including arc welding, gas welding, and resistance welding.
- Participants receive theoretical and practical training, along with hands-on experience in welding workshops.
- Upon successful completion, individuals earn recognized certification and become qualified welders.
In essence, certification and proper training play a vital role in the welding industry.
The certification process implemented by the CWB ensures the competence of welders. Different certification levels allow welders to progress and enhance their skills.
Training and qualification are essential to ensure safety, quality, and professionalism in welding.
The WETC program provides standardized training and certification to meet industry requirements.
By obtaining certification and participating in proper training programs, welders can enhance their career prospects and contribute to a safer and more efficient welding industry.
Read: The Future of Welding Jobs in Canada
Challenges and Future Developments
Discussion on the challenges faced in maintaining and updating welding standards
In order to ensure safety and quality in welding practices, the Canadian Welding Bureau (CWB) faces several challenges in maintaining and updating welding standards.
- The rapid pace of technological advancements poses a challenge in keeping up with the latest welding techniques.
- Changes in materials, equipment, and processes require regular updates to welding standards.
- Developing standards that are applicable across different industries and sectors is a complex task.
- The involvement of multiple stakeholders, including industry experts, engineers, and regulators, complicates the standard-setting process.
- Ensuring that the standards align with international codes and practices is necessary for maintaining global competitiveness.
- Regular revisions are essential to address emerging safety concerns and improve the overall efficiency of welding processes.
Overcoming these challenges requires a collaborative effort from various industry players, including researchers, manufacturers, and regulators.
Introduction of new technologies and their impact on welding standards
The advent of new technologies has revolutionized the field of welding and has significant implications for welding standards.
- Robotics and automation have the potential to improve welding accuracy, productivity, and safety.
- Advanced sensors and monitoring systems enable real-time quality control and inspection during welding processes.
- Additive manufacturing, such as 3D printing, introduces new possibilities in fabrication, demanding a reevaluation of existing standards.
- The integration of artificial intelligence and machine learning in welding systems requires guidelines to ensure their safe and optimal utilization.
As these technologies continue to evolve, the CWB needs to continuously update and develop new standards to accommodate their integration into welding practices.
Overview of ongoing efforts to improve and develop welding standards for the future
The CWB, in collaboration with industry stakeholders, is actively involved in initiatives to improve and develop welding standards for the future.
- Regular consultations with industry experts enable the identification of emerging challenges and the provision of relevant solutions.
- The CWB conducts research and development projects to gain insights into novel welding techniques and validate their effectiveness.
- Promoting training and certification programs to ensure welders and inspectors are up-to-date with the latest standards and technologies.
- Collaboration with international organizations and participation in global standardization efforts contribute to aligning Canadian standards with international best practices.
- Continuous monitoring of industry trends and feedback from stakeholders assists in identifying areas for improvement and future development.
- Adopting a proactive approach by conducting regular reviews and revisions to welding standards to address emerging technologies and safety concerns.
By actively engaging in these efforts, the CWB aims to evolve welding standards to meet the challenges of the future and ensure the continued success of the Canadian welding industry.
Read: Welding Certifications in Canada: What You Need
Conclusion
Throughout this blog post, we have explored the importance of Canadian welding standards and their significance in ensuring safe and reliable welding practices.
We have discussed the various standards established by the Canadian Welding Bureau (CWB) and how they regulate different aspects of the welding process.
We highlighted the key requirements outlined in the standards, such as proper welder qualifications, material specifications, and inspection procedures.
Understanding and following these standards play a vital role in preventing welding failures, reducing the risk of accidents, and ensuring the quality of welded products.
It cannot be stressed enough how crucial it is for welders, welding companies, and industry professionals to adhere to Canadian welding standards.
Compliance with these standards guarantees the safety of workers, protects the integrity of structures, and upholds industry reputation.
By strictly following the standards, welders can demonstrate their competency and commitment to quality craftsmanship.
Adhering to these standards also provides assurance to clients and customers that their projects are being completed to the highest standards of safety and quality.
As the welding industry continues to evolve, it is important for professionals to stay informed about the latest updates and advancements in Canadian welding standards.
Engaging with industry organizations, attending conferences, and participating in training programs will help welders stay up to date with the best practices in the field.
By staying informed and engaged, welders can contribute to the ongoing improvement and development of welding standards.
Their expertise and feedback can help shape future revisions and ensure that the standards remain relevant and effective.
Adherence to Canadian welding standards is paramount for the welding industry’s safety, credibility, and growth.
By understanding and following these standards, welders can uphold the highest quality standards, protect lives, and contribute to the overall advancement of the welding profession.