Understanding Metal Types and Properties
Importance of Metal Selection
Choosing the right metal is crucial for successful fabrication.
Each metal type has unique properties that affect performance.
Knowing these properties helps in achieving optimal results.
Common Metal Types
Aluminum is lightweight and resistant to corrosion.
Steel offers strength and durability for various applications.
Copper has excellent electrical conductivity and malleability.
Aluminum
Aluminum is a versatile material used in many industries.
It is easy to machine and weld, making it ideal for fabrication.
Additionally, aluminum is recyclable, promoting sustainability.
Steel
Steel comes in various grades, each designed for specific uses.
High-carbon steel increases hardness, while low-carbon steel is more malleable.
Understanding these grades assists in selecting the right steel type.
Copper
Copper is prized for its superior conductivity.
This metal is often used in electrical applications and plumbing.
Moreover, copper is resistant to corrosion and tarnishing.
Properties that Matter
The tensile strength of a metal indicates its resistance to being pulled apart.
Corrosion resistance helps metals withstand environmental elements.
Thermal conductivity is crucial for materials used in heat applications.
Tensile Strength
High tensile strength ensures metals can withstand stress without breaking.
This property is vital for structural applications in construction.
Corrosion Resistance
Corrosion-resistant metals require less maintenance and have longer lifespans.
They are especially important in marine and chemical environments.
Thermal Conductivity
Good thermal conductivity allows for efficient heat transfer.
This property is critical in electrical and heating applications.
Summary of Properties
- Aluminum: Lightweight and corrosion-resistant.
- Steel: Strong and versatile.
- Copper: Excellent conductivity and malleability.
Understanding metal types and their properties is essential for fabrication.
Unlock Your Career Potential
Visualize a clear path to success with our tailored Career Consulting service. Personalized insights in just 1-3 days.
Get StartedMastering this knowledge enhances overall fabrication skills.
Essential Tools and Equipment for Metal Fabrication
Protective Gear
Always wear appropriate protective gear when working with metal.
This includes safety goggles and gloves to prevent injuries.
Additionally, use a welding helmet to protect your eyes.
Steel-toed boots offer essential foot protection in the workshop.
Hand Tools
Invest in a good set of hand tools for metal fabrication.
Common tools include hammers, pliers, and wrenches.
Consider having different types of hammers for various tasks.
Having both needle-nose and slip-joint pliers will be beneficial.
Power Tools
Power tools significantly enhance your efficiency in metal work.
A welding machine is essential for most fabrication projects.
An angle grinder helps with cutting and smoothing metal edges.
Moreover, a drill is vital for creating holes and fastenings.
Material Cutting Tools
Proper cutting tools are crucial for quality metal fabrication.
A plasma cutter is an excellent investment for precision cuts.
Additionally, a band saw can efficiently cut through thick metal sheets.
Measuring and Layout Tools
Accurate measurements are foundational in metal fabrication.
Keep a variety of measuring tapes and squares handy.
Calipers will provide precise measurements for smaller parts.
A layout fluid can help mark accurate lines on the metal surface.
Workbenches and Clamps
A sturdy workbench is necessary for all metal fabrication projects.
Ensure it has sufficient surface area for your tasks.
Clamps will secure your workpieces in place while working.
Welding Equipment
Welding equipment is essential for joining metal pieces together.
Choose between MIG, TIG, or Stick welding based on your needs.
Make sure to have adequate ventilation when welding.
This helps to remove harmful fumes and ensure workplace safety.
Storage Solutions
Effective storage solutions keep your workspace organized.
Metal storage cabinets can protect tools from damage.
Use labeled bins to store small parts and accessories.
Basic Welding Techniques Every Fabricator Should Know
Understanding Welding Processes
Welding is essential for metal fabrication work.
There are various welding processes to master.
MIG welding is popular for its ease and speed.
TIG welding provides precision for detailed work.
Stick welding is versatile and useful in various conditions.
Each process has unique advantages and limitations.
Essential Safety Practices
Safety is paramount when welding.
Wear proper protective gear, including helmets and gloves.
Ensure your workspace is well-ventilated and free of flammable materials.
Familiarize yourself with emergency safety procedures.
Maintain equipment regularly to prevent accidents.
Preparing Workpieces
Proper preparation of workpieces simplifies welding.
Clean surfaces to remove rust, paint, and grease.
Accurate measurements lead to better fit-up and alignment.
Use clamps or jigs to hold pieces securely.
Mastering Joint Configurations
Different joints require different techniques.
Butt joints are common and may be challenging for beginners.
Lap joints are straightforward and provide added strength.
Tee joints can be tricky; ensure proper alignment.
Understanding joint configuration enhances overall quality.
Practicing Control of Welding Variables
Controlling variables affects weld quality.
Adjust voltage and amperage based on material thickness.
Travel speed impacts bead appearance and penetration.
Consistency in your technique leads to effective results.
Finishing and Inspection Techniques
Finishing requires attention to detail.
Remove slag and spatter to enhance appearance.
Inspect welds for strength and defects.
Testing methods help ensure weld integrity.
Explore Further: Insights into Construction Laws for Bricklayers
Blueprint Reading and Technical Drawing Interpretation
Importance of Blueprint Reading
Blueprint reading is crucial for every metal fabricator.
This skill enables fabricators to understand complex designs.
Accurate interpretation of blueprints minimizes errors.
Moreover, it ensures safety during fabrication processes.
Key Elements of Blueprints
Blueprints typically include various essential elements.
Dimensions provide accurate measurements for parts.
Notes clarify specifications and fabrication processes.
Symbols represent specific materials and finishes.
Understanding scales allows for precise scaling in real life.
Technical Drawings Explained
Technical drawings play a vital role in fabrication.
They provide detailed information on assembly and installation.
Fabricators must learn to read multiple types of drawings.
Common types include orthographic, isometric, and exploded views.
Developing Interpretation Skills
To master blueprint reading, practice is essential.
Start with simpler drawings before progressing to complex ones.
Utilize resources like textbooks and online tutorials.
Joining study groups promotes collaborative learning.
Tools to Aid Understanding
Various tools assist in interpreting blueprints effectively.
A scale ruler helps in measuring dimensions accurately.
Graphite pencils allow for clear marking and notes.
Software programs can aid in viewing digital blueprints.
Real-World Applications
Blueprint reading skills apply directly to fabrication tasks.
In a shop setting, clarity leads to better teamwork.
Accurate readings decrease waste and improve efficiency.
Ultimately, these skills lead to high-quality output.
You Might Also Like: Exploring the Day-to-Day Tasks of an Ironworker
Safety Practices and Procedures in Metal Fabrication
Understanding the Importance of Safety
Safety is crucial in metal fabrication.
It protects workers from injuries and accidents.
Moreover, implementing safety practices fosters a productive work environment.
Personal Protective Equipment (PPE)
Wearing the right personal protective equipment is essential.
Always use safety glasses to protect your eyes.
Ear protection is necessary to prevent hearing loss.
Additionally, gloves guard against cuts and abrasions.
Appropriate footwear prevents foot injuries from heavy materials.
Workplace Organization
A well-organized workspace promotes safety.
Keep tools and materials stored properly to minimize hazards.
Regularly clean your workspace to remove potential trip hazards.
Labeling storage areas ensures easy access to necessary items.
Awareness of Surroundings
Stay alert and aware of your surroundings while working.
Monitor for potential hazards like overhead equipment or moving vehicles.
Communicate effectively with coworkers about tasks and movements.
Report any unsafe conditions to a supervisor immediately.
Proper Handling of Tools and Equipment
Use tools and equipment according to manufacturer’s instructions.
Inspect tools for defects before each use.
Never use damaged tools as they can cause accidents.
Follow proper lifting techniques to avoid injuries.
Emergency Preparedness
Know the location of emergency exits and first aid kits.
Participate in regular safety drills to prepare for emergencies.
Understand how to respond to various emergencies, such as fires or chemical spills.
Keep contact information for emergency services readily accessible.
You Might Also Like: Key Tools Used by Professional Metal Fabricators
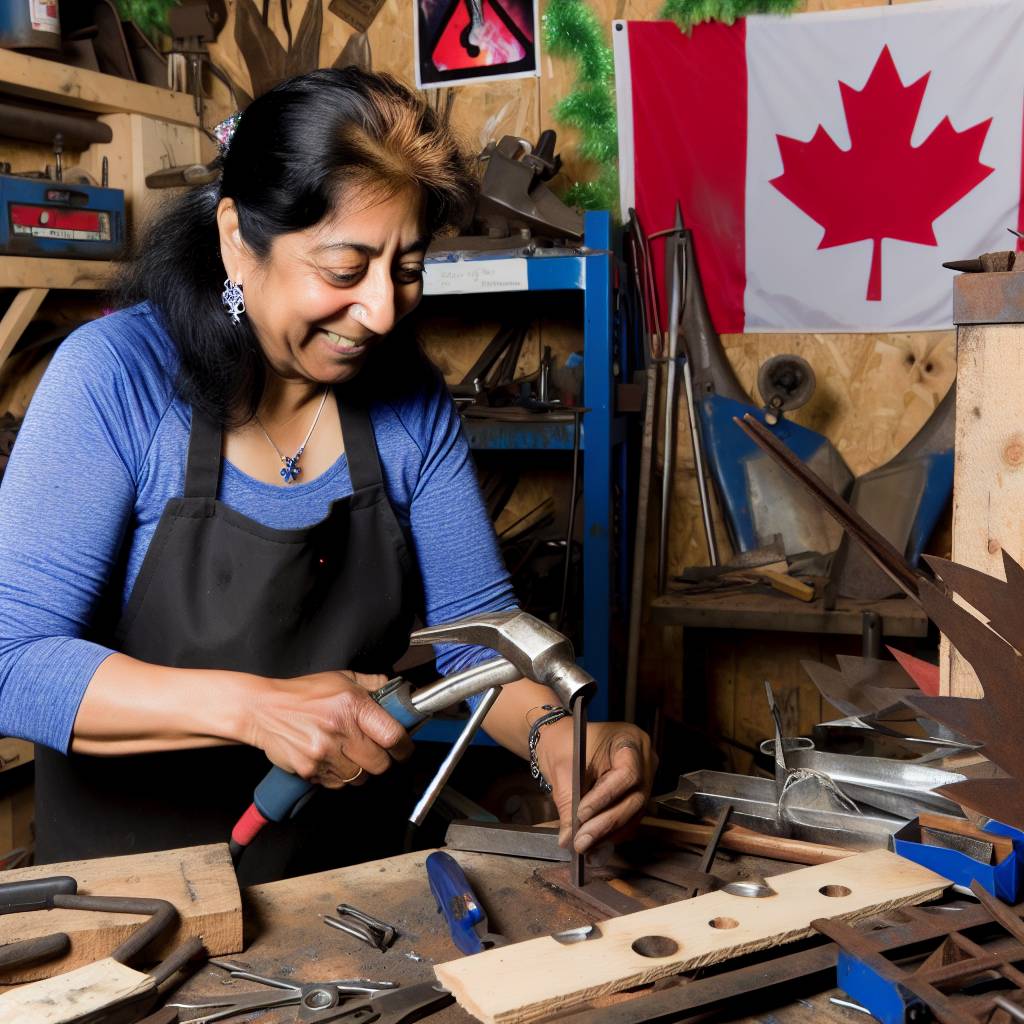
Precision Measurement and Quality Control Techniques
The Importance of Precision Measurement
Precision measurement is vital in metal fabrication.
It ensures accuracy in cutting, bending, and assembling materials.
Moreover, it helps prevent costly errors during production.
Using precise tools also leads to better product quality.
In turn, this boosts customer satisfaction and trust.
Key Measuring Tools
Fabricators must master various measuring tools.
Common tools include calipers, micrometers, and lasers.
Calipers measure external and internal dimensions effectively.
Micrometers provide precise thickness measurements.
Laser systems facilitate accurate distance measurements over larger areas.
Understanding Tolerances
Tolerances define the acceptable range of measurements.
Fabricators need to understand tolerance specifications clearly.
They must ensure their work stays within these limits.
Meeting tolerance requirements affects the final product’s performance.
Additionally, it impacts production efficiency and waste reduction.
Quality Control Techniques
Quality control is essential for maintaining high standards.
Regular inspections throughout the fabrication process are critical.
Implementing checklists can streamline quality assessments.
Fabricators should use Statistical Process Control (SPC) to track variations.
Feedback loops help identify recurring issues quickly.
Utilizing Industry Standards
Adhering to industry standards ensures consistent quality.
Standards provide guidelines for measurement and testing methods.
Organizations like ISO and ASTM offer valuable resources.
Fabricators should stay updated with changes in these standards.
Training and Continuous Improvement
Ongoing training helps fabricators master measurement techniques.
Workshops and certifications can deepen their knowledge.
Encouraging a culture of continuous improvement benefits everyone.
This approach leads to better efficiency and output quality.
Ultimately, skilled fabricators enhance the reputation of their companies.
Discover More: Challenges and Rewards of Residential Roofing Jobs
Advanced Fabrication Techniques
CNC Machining
CNC machining remains a cornerstone of modern metal fabrication.
This technology utilizes computer-controlled tools for precise cuts.
First, operators must understand CAD software for design.
Next, familiarity with various machining tools is crucial.
Operators benefit from knowledge of milling, drilling, and turning.
Also, understanding material properties improves machining outcomes.
Safety practices are essential when working with heavy machinery.
Regular maintenance ensures CNC machines operate efficiently.
Finally, staying updated on technological advancements enhances skills.
Laser Cutting
Laser cutting has transformed the metal fabrication landscape.
This technique delivers precision and speed in material processing.
Knowledge of different laser types is vital for effective use.
Operators should understand the capabilities of CO2 and fiber lasers.
Additionally, familiarity with CAD and CAM software is advantageous.
Correctly setting parameters ensures optimal cutting quality.
Material thickness greatly influences the performance of laser cutting.
Regular inspection of laser equipment minimizes unexpected issues.
Moreover, learning about safety protocols is paramount in operations.
Problem-Solving and Critical Thinking Skills in Fabrication Projects
The Importance of Problem-Solving Skills
Problem-solving is essential in metal fabrication.
Every project presents unique challenges.
Therefore, fabricators must think critically to overcome obstacles.
For instance, unexpected material defects can arise.
In addition, tight deadlines may force quick decision-making.
Consequently, effective problem solvers can maintain productivity.
Developing Critical Thinking Abilities
Critical thinking enhances a fabricator’s decision-making process.
It involves analyzing information thoroughly before concluding.
Moreover, evaluating different approaches can lead to better solutions.
For example, comparing the costs and benefits of various techniques is vital.
This helps in selecting the most efficient method for the project.
Ultimately, critical thinking reduces waste and saves time.
Practical Steps to Enhance Problem-Solving Skills
A variety of strategies exist to improve problem-solving capabilities.
- Regularly engage in hands-on practice to build experience.
- Seek feedback from others, including peers and mentors.
- Study common problems in fabrication to anticipate issues.
- Work on complex projects that challenge your current skill set.
These practices can significantly enhance your abilities over time.
Case Studies of Successful Problem Solving
Examining real-world scenarios can provide valuable insights.
For instance, a fabrication company may face supply chain disruptions.
They successfully proposed alternative suppliers to mitigate the issue.
Furthermore, analyzing how others overcame similar challenges is beneficial.
Learning from past experiences can inspire innovative solutions.
Thus, success stories serve as important learning tools.
Additional Resources
Upcoming Events and Media Announcements – Aspire Trade High …