Introduction to Modern Metal Fabrication Techniques
Modern metal fabrication encompasses various innovative techniques.
These techniques evolve constantly, driven by technology advances.
Businesses now utilize automation and robotics for efficiency.
This transformation leads to faster production and reduced costs.
Moreover, precision in metalworking has reached new heights.
Adoption of Advanced Machinery
Modern facilities frequently integrate CNC machinery into their operations.
CNC stands for Computer Numerical Control.
Such machinery enhances accuracy and repeatability significantly.
In addition, it allows for complex designs to be achieved easily.
Utilization of Laser Cutting
Laser cutting systems have revolutionized the metal fabrication landscape.
This technique offers precise cuts with minimal material waste.
Additionally, it accommodates a wide range of materials effectively.
For example, steel, aluminum, and brass can all be processed using lasers.
Emphasis on Sustainability
Modern businesses prioritize sustainable practices in fabrication.
They implement recycling programs for metal scrap, reducing waste.
Energy-efficient machinery further minimizes the environmental impact.
This commitment to sustainability attracts eco-conscious consumers as well.
Collaboration with Software Innovations
Advanced software now aids designers in metal fabrication projects.
CAD software allows for exceptional design versatility and precision.
Furthermore, simulations enable better planning before actual production.
This leads to fewer errors and higher quality outputs.
Overview of Innovative Technologies in Metalworking
Advanced Machining Techniques
Modern metalworking employs various advanced machining techniques.
These methods include Computer Numerical Control (CNC) machining.
CNC machining enhances precision and reduces human error.
Moreover, laser cutting technology streamlines the fabrication process.
Unlock Your Career Potential
Visualize a clear path to success with our tailored Career Consulting service. Personalized insights in just 1-3 days.
Get StartedThis technology provides clean cuts with minimal material wastage.
3D Printing Innovations
3D printing has revolutionized metal fabrication.
This technique allows for complex geometries that traditional methods cannot achieve.
Additionally, 3D printing reduces lead times significantly.
It promotes customization and small-batch productions effortlessly.
Automation in Metalworking
Automation plays a vital role in modern metalworking.
Robotics improve efficiency and safety on the shop floor.
Automated systems handle repetitive tasks with precision.
As a result, workers can focus on more complex operations.
Smart Manufacturing Solutions
Smart manufacturing integrates the Internet of Things (IoT) with metalworking.
IoT facilitates real-time monitoring of machinery and processes.
This connectivity enhances decision-making and operational efficiency.
Furthermore, data analytics supports predictive maintenance strategies.
Environmental Considerations in Metalworking
Innovative technologies focus on sustainability in metalworking.
Techniques like recycling scrap metal reduce environmental impacts.
Moreover, energy-efficient processes minimize energy consumption during fabrication.
These practices contribute to a greener manufacturing future.
Additive Manufacturing: Revolutionizing Metal Fabrication
Introduction to Additive Manufacturing
Additive manufacturing (AM) transforms traditional metal fabrication methods.
This technique builds objects layer by layer from digital models.
It contrasts sharply with subtractive methods, which remove material.
AM offers new opportunities for design complexity and customization.
Benefits of Additive Manufacturing
Additive manufacturing provides significant advantages in various industries.
It reduces material waste considerably.
This process utilizes only the necessary amount of material.
Moreover, it allows for rapid prototyping and quicker production times.
Custom parts can be created without the need for extensive tooling.
Applications of Additive Manufacturing in Metal Fabrication
Additive manufacturing finds applications across multiple sectors.
In aerospace, it produces lightweight components while maintaining strength.
This approach is crucial for achieving fuel efficiency and performance.
In the automotive industry, manufacturers customize parts for optimal design.
Medical devices also benefit, as implants can be tailored to individual patients.
Challenges and Future of Additive Manufacturing
Despite its benefits, additive manufacturing faces challenges.
Quality control remains a significant concern for manufacturers.
Standards and regulations are still evolving in this area.
However, advancements in technology may soon resolve these issues.
The future of additive manufacturing looks promising, with ongoing research.
This sector continues to push the boundaries of what is possible.
Find Out More: Top Tools Essential for Bricklayers in Canada
Robotics and Automation in the Fabrication Process
Enhancing Precision and Efficiency
Robotics has transformed metal fabrication by improving precision.
Automated systems deliver consistent quality with minimal human error.
Additionally, robots can perform repetitive tasks faster than human workers.
This efficiency reduces production times significantly.
As a result, manufacturers can meet increased demand without sacrificing quality.
Integration of Advanced Technologies
Modern metal fabrication incorporates advanced technologies alongside robotics.
3D printing, for example, enables rapid prototyping and design flexibility.
Laser cutting technology enhances cutting precision and minimizes waste.
Furthermore, artificial intelligence helps optimize production workflows.
Automation systems learn from data, continuously improving overall performance.
Impact on Workforce Dynamics
The rise of automation has shifted workforce dynamics in the industry.
While some jobs are replaced, new roles emerge focusing on tech oversight.
Workers now need training in robotics and computer programming.
Companies strive to balance technology use with skilled labor demands.
This creates a hybrid workforce capable of adapting to technological changes.
Examples of Leading Companies
Several companies are pioneering innovations in metal fabrication.
For instance, Alpha Metal Works implements robotic welding for efficiency.
Meanwhile, Beta Fabrications incorporates automated laser systems in production.
These companies showcase the future of manufacturing with robotics.
They demonstrate how technology enhances productivity and quality.
See Related Content: Key Safety Practices for HVAC Technicians on the Job
Laser Cutting and Its Applications in Metal Fabrication
Introduction to Laser Cutting Technology
Laser cutting revolutionizes the metal fabrication industry.
This method utilizes highly focused laser beams to cut through materials.
It provides high precision and accuracy for intricate designs.
Moreover, it minimizes material wastage during the cutting process.
Advantages of Laser Cutting
Laser cutting offers several distinct advantages over traditional methods.
First, it produces clean edges with minimal burrs or slag.
Consequently, this reduces the need for secondary finishing processes.
Second, it excels in cutting thin and thick materials alike.
Additionally, laser cutting has a high speed, enabling quick production times.
Applications in Different Industries
Laser cutting finds applications across various sectors.
In the automotive industry, it helps shape complex components.
The aerospace sector benefits from lightweight, precise parts created by lasers.
Moreover, the electronics industry relies on laser cutting for circuit board fabrication.
Innovative Uses of Laser Cutting
Innovation in laser cutting continues to emerge.
For instance, laser etching allows for detailed markings on metal surfaces.
Furthermore, 3D laser cutting techniques enable advanced sculpting capabilities.
These innovative uses drive efficiency and open new design possibilities.
Future Trends in Laser Cutting
The future of laser cutting appears promising.
Advancements in technology are leading to faster and more efficient lasers.
Additionally, automation and AI integration will enhance precision capabilities.
As a result, industries can expect continuous improvements in productivity.
See Related Content: Upholstery Repair vs Replacement What to Advise Clients
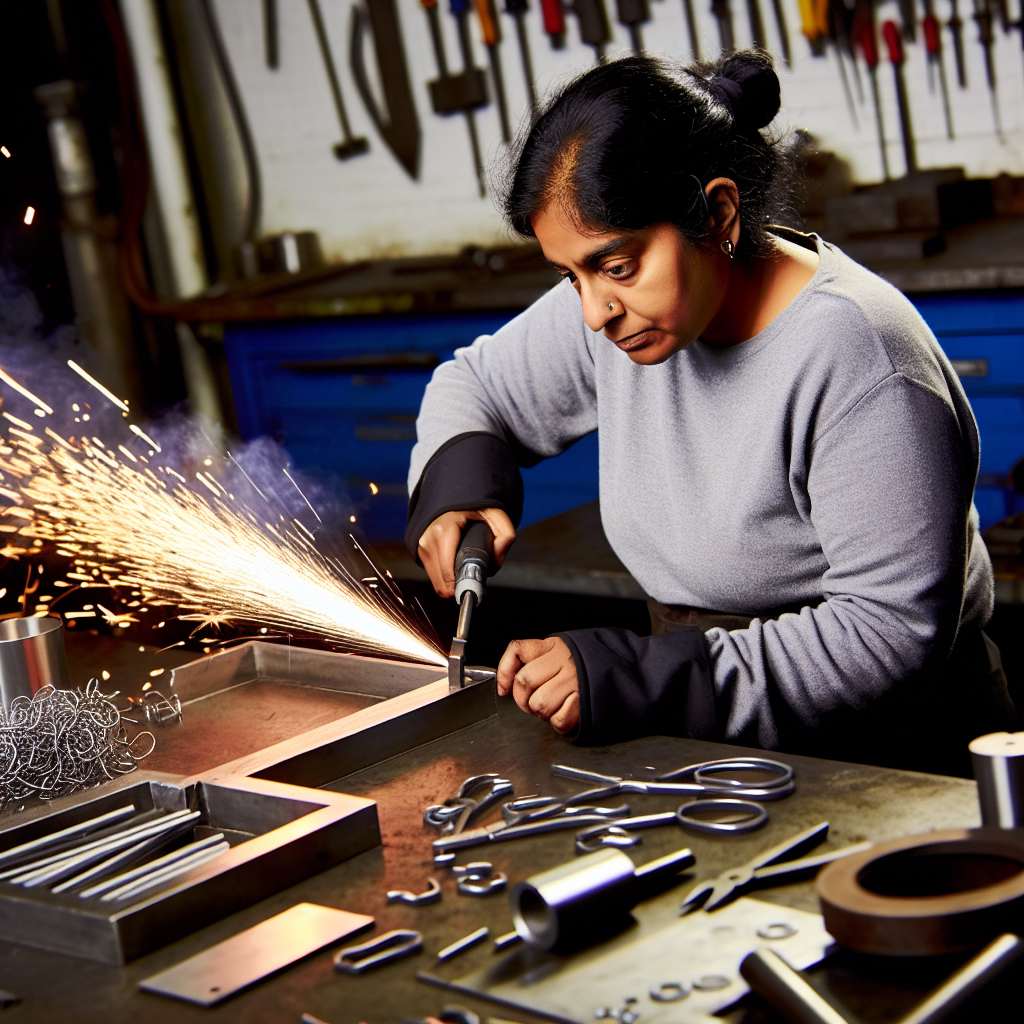
3D Printing of Metals and Its Impact on Customization
Overview of 3D Metal Printing
3D printing has revolutionized metal fabrication significantly.
It enables rapid prototyping and manufacturing of complex designs.
Moreover, it uses additive techniques to create parts layer by layer.
This process differs from traditional subtractive manufacturing methods.
Consequently, it reduces material waste and production costs.
Customization Capabilities
One of the most notable advantages is customization.
Manufacturers can produce unique parts tailored for specific needs.
This capability allows users to modify dimensions easily.
Furthermore, metal properties can also be adjusted during production.
As a result, businesses can adapt quickly to market demands.
Applications in Various Industries
3D metal printing finds applications in numerous sectors.
Aerospace is one of the most prominent industries benefiting greatly.
Companies like Boeing use this technology for lightweight components.
Additionally, the automotive industry explores custom parts for performance.
Medical applications also include patient-specific implants and tools.
Challenges and Considerations
Despite its advantages, challenges exist in the adoption of this technology.
Often, initial setup costs remain high for manufacturers.
Furthermore, quality control and standards still require attention.
For instance, ensuring the mechanical properties of printed metals is crucial.
Investing in proper training for personnel is also necessary.
Future Trends in Metal 3D Printing
The future of 3D printing in metals looks promising.
Advancements in materials science will lead to better performance.
Additionally, software innovations will streamline design processes.
Companies will likely continue exploring new applications and markets.
Overall, customization remains at the forefront of this evolving field.
You Might Also Like: HVAC Technician Salary Expectations and Benefits
The Role of CAD/CAM Software in Modern Fabrication
Introduction to CAD/CAM Software
CAD/CAM software revolutionizes the metal fabrication industry.
It combines design and manufacturing processes seamlessly.
This software enables precision and efficiency in production.
Benefits of CAD/CAM Software
CAD/CAM software significantly optimizes design workflows.
It allows for rapid prototyping and testing of designs.
This software reduces material waste through precise cutting paths.
Moreover, it minimizes errors in the fabrication process.
Integration with Modern Tools
Modern CAD/CAM software integrates well with CNC machines.
It automates machining processes, enhancing productivity.
This integration ensures consistent quality in fabricated parts.
Real-World Applications
Various industries utilize CAD/CAM software for metal fabrication.
Aerospace companies rely on it for complex component designs.
Automotive manufacturers benefit from its efficiency and accuracy.
Additionally, architectural firms use it for intricate metal designs.
Future Trends in CAD/CAM Technology
Artificial intelligence is emerging in CAD/CAM software.
This technology will enable smarter design choices.
Furthermore, cloud computing enhances collaboration among teams.
These trends promise to drive innovation in the fabrication sector.
Sustainability in Metal Fabrication: Innovative Practices and Technologies
Overview of Sustainable Practices
Sustainable practices in metal fabrication focus on reducing environmental impact.
They aim to minimize waste and conserve resources.
These practices involve using recycled materials and eco-friendly processes.
Use of Recycled Materials
Recycling metal reduces the need for virgin resources.
This process saves energy and lowers greenhouse gas emissions.
Companies like GreenCycle Metals excel in using post-consumer scrap.
They transform waste into valuable raw materials for fabrication.
Efficient Energy Use
Energy-efficient technologies have become vital in modern plants.
Advanced machinery consumes less power while maintaining high performance.
For instance, laser-cutting techniques reduce energy waste significantly.
Additionally, the use of renewable energy sources is increasing.
Water Conservation Techniques
Water is a crucial resource in metal fabrication processes.
Innovative cooling systems recycle water to minimize consumption.
Companies are also implementing closed-loop water systems.
This approach reduces water usage and prevents pollution effectively.
Implementation of Green Manufacturing Standards
Many firms now adhere to green manufacturing standards.
Standards like ISO 14001 emphasize continuous environmental improvement.
By achieving these certifications, companies showcase their commitment.
This enhances their marketability and reputation.
Impact of Technology on Sustainability
Emerging technologies drive sustainability in metal fabrication.
Industry 4.0 concepts like IoT and big data optimize operations.
These technologies improve resource management and waste reduction.
Companies can analyze data for better decision-making and efficiency.
Case Studies of Successful Implementation
Many companies illustrate how sustainability can be effectively applied.
For example, Steel Innovations has drastically reduced its carbon footprint.
They employ a zero-waste strategy and recycle 90% of their materials.
This initiative has garnered industry acclaim and customer loyalty.
Future Trends in Sustainable Metal Fabrication
Looking ahead, trends indicate increased investment in green technologies.
Automation and smart processes will further enhance sustainability.
Moreover, regulations will likely evolve, promoting eco-friendly practices.
Staying ahead requires companies to adopt innovative solutions.
Additional Resources
NAFTA and the USMCA: Weighing the Impact of North American Trade