Key Responsibilities of a Metallurgical Engineer
Researching Metal Properties
Metallurgical engineers conduct detailed research on various metals.
They analyze properties such as strength, hardness, and ductility.
This research helps in understanding how metals behave under different conditions.
Furthermore, engineers assess how alloys perform compared to pure metals.
Testing and Experimentation
Engineers design experiments to test material properties.
They utilize state-of-the-art equipment for accurate measurements.
This testing helps evaluate how metals will perform in real-world applications.
Through experimentation, they can identify potential weaknesses in materials.
Material Selection
Another critical responsibility is selecting appropriate materials for projects.
Engineers consider factors like cost, availability, and performance requirements.
They ensure that chosen materials meet industry standards.
This selection process is crucial for the success of engineering projects.
Collaboration with Other Professionals
Metallurgical engineers often work closely with design teams.
They provide insights on material capabilities and limitations.
Collaborating with production teams ensures manufacturability of designs.
Engineers must communicate technical findings effectively to non-experts.
Quality Control and Assurance
Engineers implement stringent quality control measures throughout the material lifecycle.
They monitor production processes to maintain high standards.
Regular inspections help in identifying defects early.
This proactive approach minimizes waste and enhances product reliability.
Continuous Improvement
Metallurgical engineers are responsible for pursuing advancements in metal technologies.
They analyze existing processes for efficiency improvements.
By staying updated with industry trends, engineers introduce innovative techniques.
This dedication to improvement drives progress in metallurgical engineering.
Developing and Implementing Metal Processing Techniques
Understanding Metal Processing Techniques
Metal processing encompasses various techniques like casting, forging, and heat treatment.
Unlock Your Career Potential
Visualize a clear path to success with our tailored Career Consulting service. Personalized insights in just 1-3 days.
Get StartedEach method serves unique purposes in the manufacturing process.
Metallurgical engineers play a crucial role in selecting the right technique.
Implementing Casting Techniques
Casting involves pouring molten metal into molds.
This technique creates intricate shapes and designs with high precision.
Metallurgical engineers must ensure the right alloy is used for desired properties.
They also oversee cooling rates to minimize defects.
Utilizing Forging Methods
Forging reshapes metal using compressive forces.
It enhances the metal’s strength and toughness.
Engineers must select the appropriate temperature and tooling for effective forging.
Additionally, they monitor the process to ensure quality and consistency.
Applying Heat Treatment Processes
Heat treatment alters the physical and sometimes chemical properties of metals.
It can improve hardness, strength, and corrosion resistance.
Engineers design heat treatment cycles tailored to specific metals and applications.
They also assess the impact of these processes on the material’s microstructure.
Continuous Improvement and Innovation
Metallurgical engineers regularly seek advancements in processing techniques.
They conduct experiments to evaluate new materials and methods.
This commitment to innovation leads to enhanced efficiency and product quality.
Furthermore, they collaborate with cross-functional teams to implement new technologies.
Compliance and Safety Standards
Metallurgical engineers ensure that all processes meet industry standards.
They adhere to safety regulations to protect workers and equipment.
Regular training and updates on best practices are essential in this field.
This vigilance promotes a safe working environment and operational efficiency.
Designing Processes for the Extraction of Metals
Understanding Metallurgy
Metallurgical engineering involves the study of metals and their properties.
This field focuses on both extraction and processing.
Metallurgists analyze the structure of materials to optimize their use.
Extraction from Ores
The first step is identifying suitable ores for extraction.
Metallurgical engineers evaluate the accessibility and composition of ores.
They design methods to efficiently extract metals from these ores.
In this phase, engineers often develop new extraction techniques.
They must consider environmental impacts during extraction.
Refining Processes
Once metals are extracted, engineers refine them for purity.
This involves removing impurities and enhancing material properties.
Techniques like smelting and electrolysis are commonly employed.
Refining is critical to ensure metals meet industrial standards.
Industry Collaborations
Metallurgical engineers work closely with mining companies.
They ensure that extraction processes are economically viable.
Additionally, collaboration with manufacturers helps adapt processes for specific applications.
Such partnerships drive innovation in metallurgical practices.
Research and Development
Ongoing research plays a crucial role in metallurgy.
Engineers explore new materials and technologies regularly.
This research helps improve extraction and refining efficiency.
Ultimately, it contributes to sustainable practices in the industry.
Uncover the Details: Why Chemical Engineering Is a High-Demand Career
Testing and Analyzing Metal Samples
Understanding Sample Quality
Metallurgical engineers play a vital role in assessing metal quality.
They evaluate samples by conducting various tests.
These tests help identify physical and chemical properties.
Additionally, engineers ensure metals meet industry standards.
Sample Preparation
Proper sample preparation is essential for accurate results.
First, engineers cut samples to suitable sizes.
Next, they clean samples to remove contaminants.
Then, they label each sample for identification purposes.
Testing Methods
Engineers employ several testing methods to analyze metal samples.
- Tensile testing evaluates material strength.
- Hardness testing measures resistance to deformation.
- Corrosion testing assesses material durability in hostile environments.
- Microscopy examines the microstructure of metals.
Data Analysis and Interpretation
After testing, engineers analyze the collected data.
They interpret results to identify any quality issues.
This analysis informs decisions regarding material suitability.
Engineers also prepare detailed reports based on their findings.
Applications in Industry
Understanding metal quality is crucial for various applications.
In aerospace, high-quality materials ensure safety and performance.
In automotive, they enhance vehicle durability and efficiency.
Furthermore, manufacturing processes depend on reliable material properties.
Find Out More: Salary Expectations for Chemical Engineers in Canada
Collaborating with Cross-Functional Teams to Solve Manufacturing and Material-Related Problems
Importance of Collaboration
Collaboration is essential in the role of a metallurgical engineer.
It enables engineers to address complex challenges effectively.
Working with diverse teams fosters innovation and creativity.
Engaging with Manufacturing Teams
Metallurgical engineers work closely with manufacturing teams.
They help streamline processes to improve product quality.
Additionally, they troubleshoot material-related issues during production.
This proactive engagement reduces downtime and enhances output.
Interacting with Product Design Teams
Collaboration with product design teams is crucial.
Metallurgical engineers provide insights on material selection.
They ensure designs meet mechanical property requirements.
This coordination helps avoid costly design modifications later.
Coordinating with Quality Assurance Teams
Cohesive work with quality assurance teams is vital.
Metallurgical engineers help set testing standards for materials.
They evaluate results to guarantee compliance with specifications.
This ensures products meet required quality levels consistently.
Collaborating with Research and Development
Partnerships with R&D teams drive innovation in materials science.
Metallurgical engineers contribute to the development of new alloys.
They explore advanced manufacturing techniques to enhance performance.
Moreover, they stay updated on the latest industry advancements.
Building Effective Communication Channels
Effective communication enhances collaboration among teams.
Metallurgical engineers should foster open dialogue and feedback.
This promotes an inclusive atmosphere where ideas can flourish.
Furthermore, regular meetings can keep all parties informed.
Case Studies of Successful Collaborations
Studying successful collaborations can offer valuable insights.
Many companies have improved efficiency through teamwork.
For example, TechMet Solutions increased production yield by 25%.
Their metallurgical engineers worked closely with manufacturing staff.
This collaborative approach resolved material failure issues swiftly.
Explore Further: Education Path for Aspiring Metallurgical Engineers
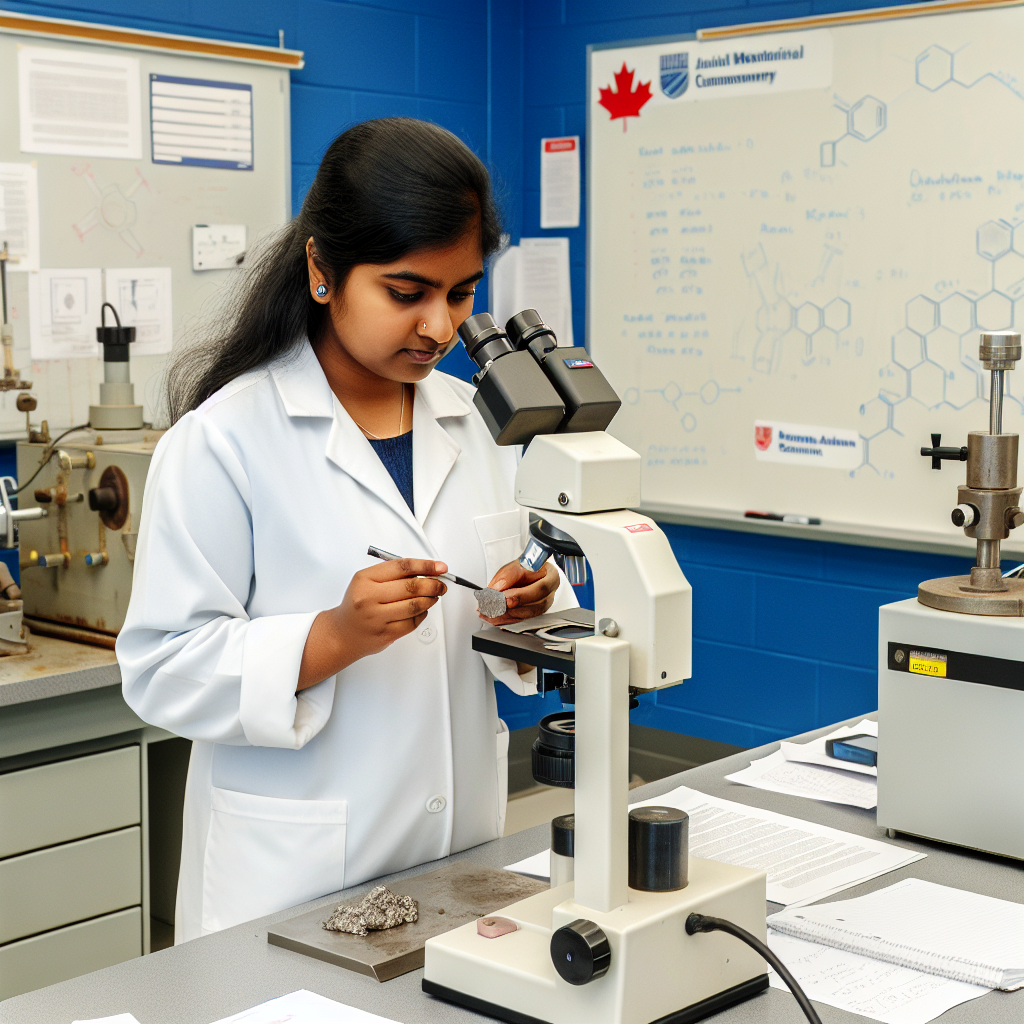
Evaluating the Environmental and Economic Impacts of Metallurgical Processes and Materials
Understanding Environmental Impacts
Metallurgical processes can significantly affect the environment.
They often involve the use of various chemicals and materials.
These agents can lead to soil and water contamination.
Metallurgical engineers must assess these environmental risks actively.
They employ tools to monitor pollution levels effectively.
Implementing sustainable practices is crucial in this domain.
For instance, recycling metals reduces the demand for raw materials.
This practice decreases energy consumption and waste generation.
Economic Implications of Metallurgical Processes
Economics plays a vital role in metallurgical engineering.
Engineers must consider the cost-effectiveness of processes.
They analyze how resources are allocated within production cycles.
Efficiency in extraction and processing can enhance profitability.
Engineers often collaborate with manufacturers to optimize operations.
Developing cost-reduction strategies can lead to competitive advantages.
Balancing Environmental and Economic Goals
Finding a balance between environmental stewardship and economic viability is essential.
Metallurgical engineers evaluate sustainable technologies to achieve this goal.
Innovative practices can minimize environmental footprints while maximizing profit.
Such efforts ensure compliance with regulations and community standards.
Additionally, these practices can improve a company’s public image.
Ultimately, responsible engineering benefits both the environment and the economy.
Case Studies in Sustainable Metallurgy
Several companies have successfully implemented sustainable practices.
For example, Acme Metalworks adopted a closed-loop system for production.
This system significantly reduced waste and resource consumption.
Such initiatives prove that environmental considerations can align with profit margins.
Furthermore, Abundant Resources incorporated renewable energy sources.
This decision not only cut costs but also minimized their carbon footprint.
These case studies provide valuable models for future metallurgical practices.
Explore Further: The Role of Chemical Engineers in Sustainability
Creating Detailed Documentation and Reports
Importance of Accurate Documentation
Accurate documentation is vital in metallurgical engineering.
It ensures that all processes remain transparent and repeatable.
Furthermore, it supports compliance with industry regulations.
Components of Effective Reports
Effective reports include various key components.
They should start with a clear objective statement.
Next, they outline methodologies used in experiments.
In addition, reports should present findings in detail.
Data analysis must be clear and well-supported.
To conclude, recommendations should be actionable and specific.
Maintaining Clarity and Consistency
Clarity and consistency enhance the readability of reports.
Engineers should use standard terminology consistently.
This avoids confusion and misinterpretation among readers.
Additionally, visuals like charts and graphs improve understanding.
Ensuring Timeliness in Reporting
Timely reporting is crucial in the metallurgical field.
It allows stakeholders to make informed decisions quickly.
Regular updates help in tracking progress and challenges.
Deadlines should be established to maintain momentum.
Staying Updated with Advancements in Metallurgical Technology
The Importance of Continuous Learning
Metallurgical engineers must embrace continuous learning.
This field evolves rapidly with new materials and technologies.
Staying informed helps improve production processes effectively.
Engaging with Professional Communities
Joining professional societies promotes knowledge exchange.
Organizations like ASM International offer valuable resources.
Networking with peers can stimulate innovative ideas.
Participating in Continuing Education
Continuing education keeps skills sharp and relevant.
Attending workshops and seminars is beneficial.
Many universities provide specialized programs for professionals.
Utilizing Online Resources
The internet offers extensive learning materials for engineers.
Webinars and online courses provide flexible learning options.
Industry publications deliver up-to-date information on advancements.
Research and Development Collaborations
Participating in R&D projects enhances technical expertise.
Collaborations with universities drive innovation in materials science.
Such partnerships can lead to groundbreaking advancements.
Attending Industry Conferences
Industry conferences are platforms for the latest research.
Presenting research findings helps establish professional credibility.
Furthermore, conferences foster discussions on future trends.
Adapting to Technological Advances
Metallurgical engineers must adapt to new technologies.
Automation and AI are reshaping industry practices.
Embracing these changes can enhance production efficiency greatly.
Implementing Best Practices in Production
Staying informed helps implement best practices in manufacturing.
Efficiency gains can result from new techniques and materials.
Engineers should endeavor to refine existing processes continually.
Additional Resources
Electrification and Decarbonization Solutions for Industry Workshop …