Overview of the Metal Fabrication Industry
Significance in Modern Manufacturing
The metal fabrication industry plays a crucial role in manufacturing.
It provides essential components across various sectors.
Industries such as automotive, aerospace, and construction heavily rely on fabricated metal parts.
Moreover, metal fabrication supports technological advancements and innovation.
The industry ensures a reliable supply of high-quality materials.
Additionally, it enables the efficient production of complex designs.
Key Processes in Metal Fabrication
Metal fabrication involves several key processes.
These include cutting, bending, and welding.
Each process contributes to transforming raw materials into finished products.
Cutting can involve techniques like laser or plasma cutting.
Bending shapes the metal according to specific requirements.
Welding joins different pieces together to form a single structure.
As a result, these processes enhance product durability and reliability.
Innovations Driving the Industry
The metal fabrication industry is witnessing rapid innovations.
Automation and robotics are significantly improving efficiency.
These technologies reduce labor costs and enhance production speed.
Furthermore, software advancements streamline the design process.
Computer-aided design (CAD) allows for precise modeling of projects.
This innovation leads to better planning and execution of fabrication projects.
As a result, manufacturers can meet the growing demand for customization.
Challenges Faced by the Industry
Despite its importance, the industry faces several challenges.
Firstly, fluctuations in raw material prices can impact profitability.
Moreover, there is a growing skill gap among the workforce.
Companies struggle to find qualified workers who understand advanced technologies.
Supply chain disruptions can also delay production timelines.
Unlock Your Career Potential
Visualize a clear path to success with our tailored Career Consulting service. Personalized insights in just 1-3 days.
Get StartedAdditionally, environmental regulations are becoming more stringent.
Compliance can increase operational costs for manufacturers.
Challenges in the Metal Fabrication Industry
Skilled Labor Shortages
The metal fabrication industry faces significant skilled labor shortages.
Many companies struggle to find qualified workers to meet their demands.
This shortage affects productivity and overall output.
Training programs often fall short of industry needs.
Younger generations may not see metal fabrication as a viable career path.
To combat this, companies must invest in training and apprenticeship programs.
Equipment Maintenance
Regular equipment maintenance presents another challenge.
Many companies overlook the importance of scheduled maintenance checks.
This neglect can lead to costly breakdowns and downtime.
Furthermore, outdated machinery often requires more frequent repairs.
Investing in modern equipment can offset maintenance challenges.
Additionally, having a dedicated maintenance team can improve reliability.
Regulatory Compliance
Staying updated with regulatory changes can be daunting.
Companies often face fines for non-compliance with safety standards.
They must continually adjust operations to meet these regulations.
This adds an extra layer of complexity to daily operations.
Implementing compliance training helps mitigate risks.
Supply Chain Disruptions
Supply chain disruptions are increasingly common in the fabrication industry.
Companies often depend on specific materials and parts for production.
Any delay in the supply chain can halt manufacturing processes.
Maintaining strong supplier relationships can help alleviate these issues.
Diversifying suppliers may also reduce dependency on single sources.
Market Volatility
Market volatility affects pricing and demand for fabricated products.
Economic fluctuations can lead to unpredictable revenue streams.
Companies may struggle to adapt to rapid changes in market conditions.
Developing flexible pricing strategies can help manage these challenges.
Moreover, forecasting demand accurately can improve operational planning.
Impact of Technological Advancements on the Metal Fabrication Process
Automation and Machinery Enhancements
Automation plays a crucial role in modern metal fabrication.
Advanced machinery increases production efficiency significantly.
For instance, laser cutting machines offer precision unmatched by manual techniques.
Moreover, automated welding systems reduce human error and improve safety.
These technologies allow for faster turnaround times on projects.
Consequently, companies can meet higher customer demands.
3D Printing and Its Influence
3D printing has transformed the metal fabrication landscape.
This technology enables the creation of complex geometries effortlessly.
Furthermore, it reduces material waste, making processes more eco-friendly.
Many design iterations become feasible during the prototyping phase.
As a result, product development times decrease significantly.
Innovative designs can emerge faster, giving companies a competitive edge.
Software Integration and Design Tools
Software advancements further enhance the design process in metal fabrication.
CAD software allows for detailed design visualization and modification.
Integrating simulation tools predicts how designs will perform under stress.
This capability reduces costly errors before production begins.
Assembly instructions and workflows can also be optimized digitally.
Ultimately, these tools improve the overall quality of the final product.
Skilled Workforce and Training
Technology changes the skills required in the metal fabrication industry.
The workforce must become proficient with advanced tools and machinery.
Training programs are vital for keeping skills updated in this evolving field.
Partnerships with educational institutions can help in skill development.
A skilled workforce can maximize the benefits of new technologies.
Consequently, organizations must invest in continuous learning opportunities.
Find Out More: Exploring Different Materials Used in Upholstery Work
Sustainability Challenges in Metal Fabrication
Waste Management Issues
Waste management poses a significant challenge in metal fabrication.
Manufacturers generate large volumes of scrap metal during production.
This waste can contribute to environmental pollution if not handled properly.
Moreover, companies often struggle to find effective disposal methods.
With rising costs, inefficient waste management strategies become unsustainable.
Therefore, businesses must prioritize developing better waste solutions.
Recycling Difficulties
Recycling in the metal fabrication industry faces several hurdles.
A large amount of scrap metal remains underutilized.
Many facilities lack adequate recycling programs for metal waste.
Additionally, the separation of different types of metals is challenging.
This process is essential for effective recycling efforts.
Companies must invest in advanced sorting technologies to improve efficiency.
Regulatory Compliance
Regulatory compliance adds another layer of complexity.
Industry regulations are becoming increasingly stringent.
Companies must ensure their operations meet environmental standards.
This often requires significant investments in new technologies.
Failure to comply can lead to hefty fines and operational delays.
Consequently, staying informed about regulations is crucial for manufacturers.
Innovative Practices
Despite these challenges, opportunities for innovation exist.
Implementing sustainable practices can lead to long-term benefits.
Adopting lean manufacturing methods minimizes waste generation.
Furthermore, encouraging a culture of sustainability within organizations fosters positive change.
By investing in employee training, companies can enhance waste management.
Ultimately, these innovations can improve overall operational efficiency.
Learn More: The Rise of Smart Construction: How Technology is Changing Trade Jobs in Canada
Rewards of Pursuing Innovation in Metal Fabrication
Increased Efficiency
Innovating in metal fabrication significantly boosts operational efficiency.
Faster production times lead to quicker turnaround on projects.
Advanced machinery reduces manual labor requirements.
Automation streamlines repetitive tasks, enhancing accuracy.
Consequently, efficiency gains translate to higher output levels.
Cost Savings
Pursuing innovation often results in substantial cost savings.
New technologies can lower material waste during fabrication.
Investing in modern equipment may reduce long-term operational costs.
Bulk purchasing and efficient processes lead to better resource allocation.
These savings empower companies to reinvest in further innovations.
Improved Product Quality
Innovation fosters improved quality in fabricated metal products.
Precision engineering contributes to tighter tolerances and finishes.
Using higher-quality materials enhances overall durability.
As a result, customer satisfaction levels increase significantly.
Moreover, consistent quality supports brand reputation and loyalty.
Competitive Advantage
Adopting innovative practices provides a competitive edge.
Companies that innovate can respond quickly to market demands.
Unique products set businesses apart from their competitors.
This differentiation attracts new customers and retains existing ones.
Ultimately, it positions the company as a market leader.
Find Out More: Understanding Welding Skills for Metal Fabricators
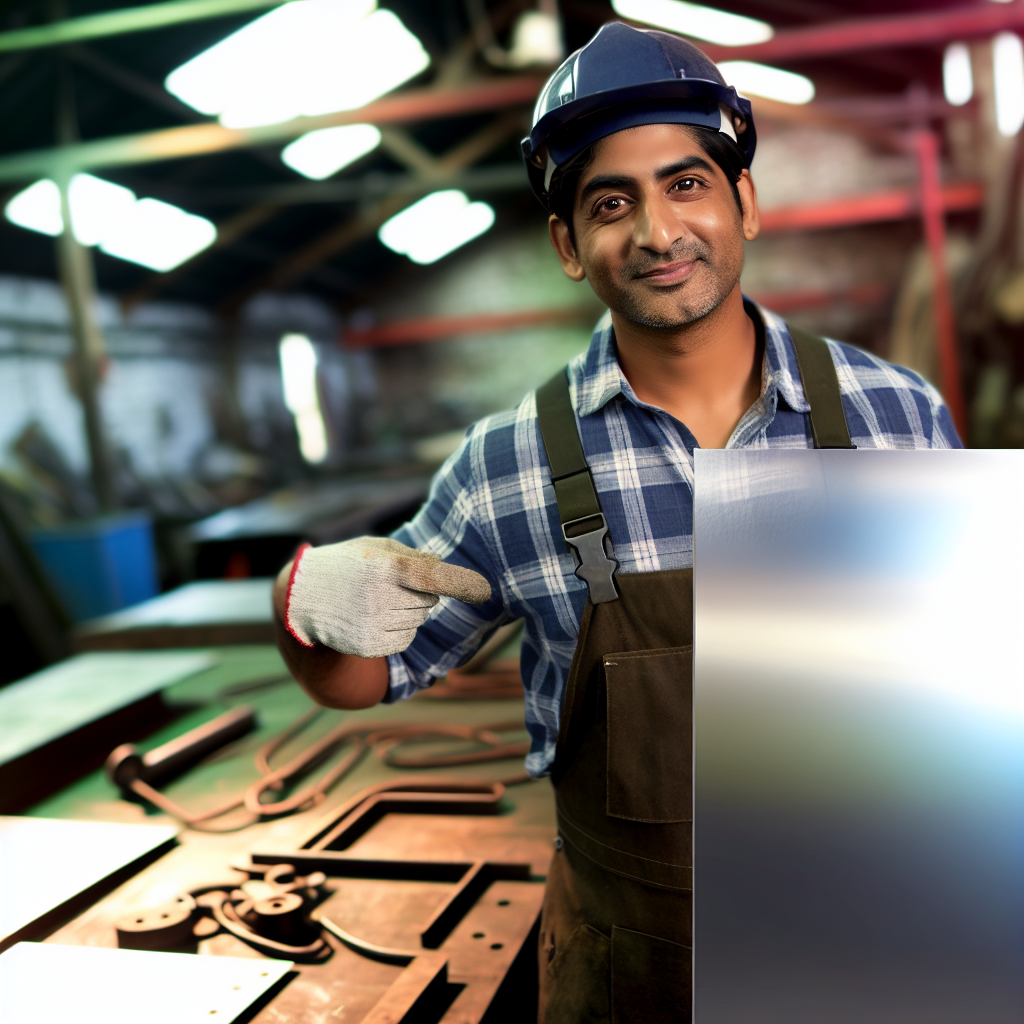
The Role of Training and Professional Development in Overcoming Industry Challenges
Addressing Skills Gap
The metal fabrication industry faces a significant skills gap.
This gap hampers productivity and innovation.
Training programs help bridge this gap effectively.
Organizations like Precision Metalforming Association promote skill development.
They offer workshops tailored to industry needs.
Enhancing Safety Protocols
Safety is paramount in the metal fabrication industry.
Regular training on safety protocols reduces workplace accidents.
Employees become more aware of potential hazards.
Moreover, training promotes a culture of safety within organizations.
Staying Current with Technology
Technology in metal fabrication evolves rapidly.
Continuous training allows employees to adapt to new tools.
Knowledge of advanced machinery greatly enhances efficiency.
As a result, professionals stay competitive in the job market.
Fostering Innovation and Creativity
Professional development encourages creative problem-solving.
Employees trained in new techniques often bring innovative ideas.
This leads to improved processes and products.
Workshops and courses foster collaboration among teams.
Building Leadership Skills
Leadership development is critical for long-term success.
Training programs often include leadership components.
These components prepare employees for supervisory roles.
Strong leaders drive organizational culture and performance.
Investing in professional development yields significant rewards.
It shapes a more skilled, safe, and productive workforce.
You Might Also Like: Exploring the Role of Metal Fabricators in Canada
Market Demand Fluctuations and Their Effects on Metal Fabrication Jobs
Understanding Market Demand
Market demand for metal fabrication fluctuates for various reasons.
Economic cycles often influence demand significantly.
As industries like automotive and construction grow, demand rises.
Conversely, economic downturns lead to decreased demand.
These fluctuations directly impact job stability in the sector.
Impact on Employment Levels
When demand rises, companies expand operations rapidly.
They increase hiring to meet production goals.
Conversely, during downturns, layoffs become common.
This volatility creates job insecurity for workers.
Additionally, companies may implement hiring freezes.
Effects on Worker Morale
Job fluctuations can negatively affect worker morale.
Employees face stress and uncertainty during downturns.
This stress can lead to decreased productivity.
On the other hand, growth periods often boost morale.
Workers feel valued and motivated during these times.
Markets Driving Demand for Fabrication
Several key markets drive demand for metal fabrication services.
The automotive industry is a major player.
Additionally, the aerospace industry also significantly impacts demand.
Construction and infrastructure projects further influence this market.
Finally, renewable energy sectors create new opportunities.
Adapting to Demand Changes
Companies must adapt to changing market demands swiftly.
Many invest in flexible manufacturing processes.
Automation and advanced technologies enhance adaptability.
Investing in skilled training for workers is also crucial.
These strategies help mitigate negative effects during downturns.
Future Prospects and Evolving Trends in the Metal Fabrication Industry
Technological Advancements
Technological innovations are reshaping the metal fabrication landscape.
Industries are increasingly adopting automation in manufacturing processes.
Advanced robotics enhance efficiency and precision in fabrication tasks.
Companies are also investing in artificial intelligence for production optimization.
Furthermore, the integration of IoT devices improves monitoring and maintenance.
Emphasis on Sustainability
Sustainability has become a key focus for metal fabrication industries.
Businesses are exploring eco-friendly materials and practices.
Energy-efficient processes significantly reduce operational costs.
Many companies are implementing recycling practices to minimize waste.
Sustainable approaches also meet consumer demands for responsible sourcing.
Workforce Development
As the industry evolves, workforce development remains crucial.
Skilled labor shortages challenge the growth of metal fabrication.
Companies are partnering with educational institutions to bridge this gap.
Apprenticeships and training programs are increasingly emphasized.
Developing a workforce skilled in new technologies is essential.
Global Market Trends
Globalization is impacting metal fabrication trends significantly.
Companies are expanding their reach to international markets.
This expansion fosters competition and drives innovation.
Moreover, trade agreements influence the cost and supply of materials.
Staying adaptable is vital for navigating these global shifts.
Customization and Specialized Services
Customization has become a priority for many clients in the industry.
Consumers seek tailored solutions to fit their unique needs.
Specialized fabrication services are emerging as an important trend.
Companies that offer niche services stand out in a competitive market.
Building strong relationships with clients enhances service delivery.
Additional Resources
U.S.-Mexico-Canada Trade Agreement: Likely Impact on the U.S. …
2025 Engineering and Construction Industry Outlook | Deloitte Insights