Understanding the Importance of Precision in Metal Fabrication
Impact on Quality
Precision dictates the overall quality of the fabricated metal product.
High precision leads to fewer defects and rework.
Moreover, it enhances the product’s durability and performance.
Cost Efficiency
Precision reduces waste of materials during the fabrication process.
This efficiency translates into lower production costs.
In turn, it can improve profitability for metal fabrication companies.
Customer Satisfaction
Customers expect high-quality products that meet their specifications.
Implementing precision ensures products fulfill these expectations.
As a result, customer loyalty and satisfaction often increase.
Safety Considerations
Precision in fabrication contributes to safety in the final product.
Defective products can pose significant safety risks.
This is particularly crucial in industries such as aerospace and automotive.
Competitive Advantage
Companies that prioritize precision stand out in a crowded market.
They can consistently deliver superior quality products.
This ability can lead to enhanced reputation and customer trust.
Key Techniques for Enhancing Fabrication Accuracy
Invest in Technology
Advanced technology significantly improves metal fabrication precision.
Consider integrating CNC machines for consistent cutting accuracy.
Moreover, using laser cutting systems enhances detail without increasing labor.
Stay updated on software developments; they streamline design and fabrication processes.
Implement Robust Quality Control
Establish a quality control program that includes regular inspections.
Utilize digital measuring tools for precise assessments.
Incorporate feedback loops for continuous improvement.
Train staff to recognize quality issues promptly.
Utilize Proper Techniques
Employ correct welding methods to ensure joint integrity.
Regularly calibrate machines to maintain optimal performance.
Unlock Your Career Potential
Visualize a clear path to success with our tailored Career Consulting service. Personalized insights in just 1-3 days.
Get StartedDon’t overlook the importance of proper material handling.
Use fixtures and jigs to maintain consistent dimensions during assembly.
Enhance Team Training
Regular training cultivates skill and precision in fabrication teams.
Encourage cross-training to expand team capabilities.
Promote a culture of accountability and attention to detail.
Provide access to workshops and courses focused on advanced techniques.
The Role of Advanced Machinery in Precision Metal Fabrication
Enhancing Accuracy with CNC Machines
Computer Numerical Control (CNC) machines have transformed metal fabrication.
They enable precise cutting, drilling, and milling of various materials.
CNC technology adheres to exact specifications for each project.
Moreover, they reduce human error, enhancing overall productivity.
Utilizing Laser Cutting Technology
Laser cutting offers exceptional precision for intricate designs.
This method creates cleaner edges and less waste compared to traditional methods.
Furthermore, laser systems can adjust settings on-the-fly, enhancing flexibility.
This adaptability allows manufacturers to meet changing project demands efficiently.
Benefits of Waterjet Machines
Waterjet cutting is another reliable method for precision fabrication.
This technique uses high-pressure water mixed with abrasives to slice through materials.
It is particularly effective on materials sensitive to high temperatures.
As a result, it eliminates the risk of thermal distortion.
Integrating Automation
Automation plays a critical role in maximizing precision and efficiency.
Automated systems streamline workflows and coordinate multiple machines.
This integration creates a seamless production environment.
Additionally, automation minimizes human intervention, reducing errors.
Implementing Quality Control Measures
Advanced machinery requires rigorous quality control processes.
Regular maintenance ensures optimal performance and longevity of equipment.
Additionally, quality assurance checks monitor production standards constantly.
This continuous oversight results in consistently high-quality outputs.
Discover More: Tips for Maintaining HVAC Systems Like a Pro
Material Selection: How It Affects Precision in Fabrication
Choosing the Right Material
Material selection is critical for achieving precision in metal fabrication.
Different metals exhibit varying properties that influence the fabrication process.
For instance, aluminum is lightweight yet strong, making it ideal for various applications.
On the other hand, stainless steel offers excellent durability and corrosion resistance.
Consequently, the chosen material can significantly impact the final product’s quality.
Understanding Material Properties
Each material possesses unique characteristics that affect precision.
Tensile strength determines how much a material can withstand without failing.
This property plays a vital role during the cutting and shaping processes.
Moreover, thermal conductivity influences how materials respond to heat treatment.
Understanding these properties helps in selecting the appropriate material for specific projects.
The Role of Thickness and Composition
The thickness of the material also impacts the precision of fabrication.
Thicker materials are often more challenging to work with and require specialized techniques.
Additionally, the composition of the metal affects its machinability and weldability.
Choosing a material with the right thickness and composition ensures accuracy in fabrication.
Evaluating Cost vs. Precision
Cost considerations often influence material selection in fabrication projects.
However, prioritizing precision can lead to better long-term outcomes.
Ultimately, it is essential to balance cost with the desired level of precision.
This approach can enhance both efficiency and product reliability.
Gain More Insights: Understanding the Daily Tasks of an HVAC Technician
Implementing Quality Control Measures in Metal Fabrication Processes
Defining Quality Control in Metal Fabrication
Quality control ensures products meet required specifications.
It focuses on minimizing defects during production.
This process enhances customer satisfaction and product reliability.
Establishing Quality Standards
Setting clear quality standards is crucial for any fabrication process.
Organizations should adopt industry standards to provide benchmarks.
ISO 9001 is a widely recognized standard for quality management.
Additionally, companies can develop internal standards based on best practices.
Incorporating Measurement Tools
Measurement tools are vital to assess precision and quality.
Calipers and micrometers provide accurate dimensional data.
Laser measurement systems can ensure accuracy in large-scale operations.
Regular calibration of tools safeguards measurement reliability.
Training Employees
Employee training plays a significant role in quality control.
Effective training programs enhance skills in operating machinery.
Workers should understand quality standards and inspection methods.
Regular workshops help keep employees updated on the latest techniques.
Implementing Inspection Processes
Inspection processes identify defects before products reach customers.
Using both manual and automated inspections can be effective.
Visual inspections should accompany measurement verification methods.
Employing checklists aids in maintaining inspection consistency.
Utilizing Statistical Process Control
Statistical process control (SPC) helps monitor production performance.
SPC utilizes data to identify trends and outliers.
This technique enables proactive adjustments to manufacturing processes.
Quality teams should analyze SPC data regularly to refine processes.
Encouraging Feedback Loops
Establishing feedback loops is essential for continuous improvement.
Technicians should report any issues encountered during production.
Management must respond to feedback promptly to resolve concerns.
Regular team meetings can facilitate open discussion about quality issues.
Conducting Root Cause Analysis
Root cause analysis identifies the underlying causes of defects.
Techniques such as the “Five Whys” help uncover issues effectively.
By addressing root causes, organizations can prevent future occurrences.
This proactive approach fosters a culture of quality awareness.
Delve into the Subject: What It’s Really Like to Be an Electrician in Canada: Day in the Life
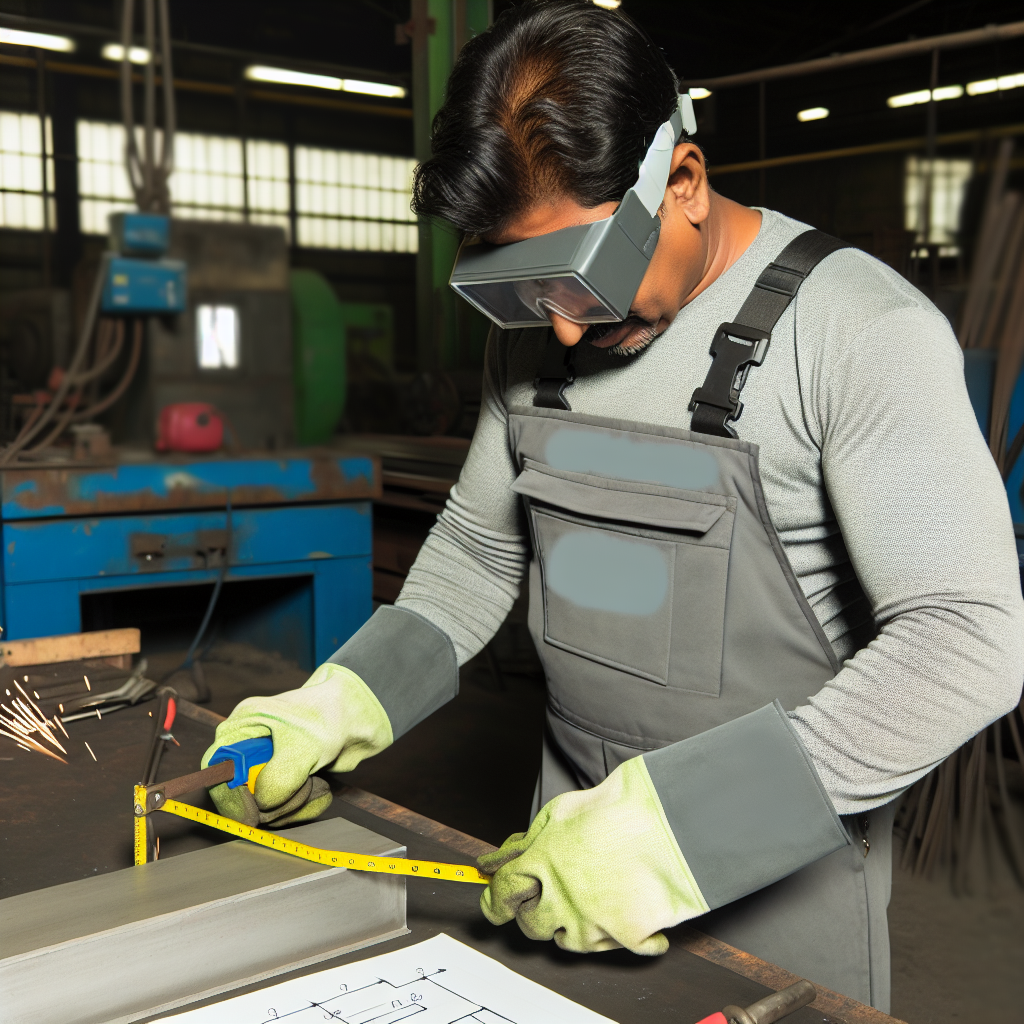
The Impact of Skilled Labor on Precision Fabrication Outcomes
The Role of Skilled Labor
Skilled labor plays a crucial role in metal fabrication.
They bring expertise and knowledge to their craft.
Furthermore, skilled workers ensure high-quality outcomes.
Training and Education
Training programs enhance workers’ skills effectively.
Education focuses on precision techniques and tools.
Consequently, well-trained workers achieve greater accuracy.
Experience Matters
Experience greatly influences fabrication outcomes.
Seasoned workers utilize their knowledge efficiently.
They quickly identify potential issues during operations.
Team Collaboration
Collaboration among skilled workers improves results.
Sharing insights fosters a culture of craftsmanship.
This teamwork enhances the overall precision of projects.
Adapting to New Technologies
Skilled labor must adapt to emerging technologies.
New tools often require additional training and practice.
Staying updated boosts fabrication quality and efficiency.
Continuous Improvement
Skilled workers engage in continuous improvement practices.
They seek feedback to refine their techniques constantly.
This mindset leads to superior precision in projects.
See Related Content: Why Skilled Labor Jobs in Canada Are the Backbone of Economic Recovery
Using CAD and CAM Software to Improve Metal Fabrication Precision
Getting Started with CAD
Computer-Aided Design, or CAD, revolutionizes metal fabrication.
This software enables precise drawings and 3D modeling.
Engineers and designers can visualize projects better with CAD.
Consequently, this leads to fewer errors during the design phase.
Using CAD increases overall efficiency across projects.
Implementing CAM Systems
Computer-Aided Manufacturing, known as CAM, automates production processes.
CAM systems interpret CAD designs and guide machinery accordingly.
This integration enhances the accuracy of production through automation.
As a result, manufacturers can create complex parts without manual error.
Benefits of CAD/CAM Integration
The integration of CAD and CAM solutions offers numerous advantages.
- Improved accuracy in metal fabrication.
- Reduced time from design to production.
- Enhanced customization options for clients.
- Streamlined data management from design to manufacturing.
Moreover, businesses can respond more quickly to market demands.
This capability can lead to greater customer satisfaction.
Choosing the Right Software
Selecting the right CAD/CAM software is crucial for success.
Evaluate options based on your specific fabrication needs.
Consider software that offers user-friendly interfaces and robust features.
Narrow down choices by examining customer reviews and case studies.
Finally, think about compatibility with existing machinery.
Training and Adoption
Training staff on new CAD/CAM software is essential.
Comprehensive training enhances employee efficiency and precision.
Utilizing online tutorials can facilitate an easier learning curve.
Additionally, regular practice leads to mastery of software functions.
Incorporate continuous learning for long-term success.
Regular Maintenance and Calibration of Equipment for Optimal Performance
Importance of Regular Maintenance
Regular maintenance keeps equipment functioning at its best.
This prevents unexpected breakdowns and costly repairs.
Moreover, well-maintained machinery operates more efficiently.
It also produces higher quality results in metal fabrication.
Key Maintenance Practices
Implement a scheduled maintenance plan for all machinery.
Inspect tools and equipment regularly for wear and tear.
Clean machinery to remove dust and debris buildup.
Lubricate moving parts to reduce friction and wear.
Replace worn-out parts promptly to avoid further damage.
Calibration for Precision
Calibration ensures that equipment performs accurately.
Regularly calibrate tools and machines according to manufacturer specifications.
This process enhances measurement accuracy during operations.
Inaccurate tools can lead to material waste and rework.
Record Keeping
Keep detailed records of maintenance and calibration activities.
This helps in tracking performance over time.
It also provides valuable data for future maintenance planning.
Employee Training
Train staff in proper equipment usage and maintenance procedures.
Knowledgeable employees can identify potential issues early.
Encourage a culture of safety and responsibility regarding equipment care.
Utilizing Professional Services
Consider hiring professionals for complex maintenance tasks.
Experts can often identify problems that might go unnoticed.
Furthermore, they can provide advanced calibration services.
This investment can save money in the long run.
Additional Resources
Gerdau Careers | Join Our Team. Shape the Future.
Should I listen to my parents to not work in this metal company due …