Introduction to Metallurgical Engineering and Resource Optimization
Metallurgical engineering focuses on the study of metals and their properties.
This field plays a crucial role in various industries, such as aerospace and automotive.
Resource optimization is essential to minimize waste and enhance efficiency.
Metallurgical engineers innovate processes to make resource usage more sustainable.
The Importance of Metallurgical Engineering
Metallurgical engineers design materials for specific applications.
They analyze metal properties like strength and ductility.
This understanding leads to better product performance and longevity.
Ultimately, their work supports the efficient use of materials.
Techniques for Resource Optimization
One technique is recycling metals from scrap materials.
This process reduces the need for raw materials significantly.
Additionally, engineers employ advanced modeling to reduce waste in production.
Implementing lean manufacturing principles enhances resource efficiency.
Impact on Sustainability
Resource optimization directly supports sustainable development goals.
By minimizing waste, metallurgical engineers contribute to environmental conservation.
Moreover, improved material efficiency leads to energy savings.
These advancements help companies reduce their carbon footprint.
Case Studies and Innovations
Several companies have successfully implemented innovative practices.
For instance, Alcoa uses advanced analytics to optimize aluminum production.
This leads to a significant reduction in energy consumption.
Similarly, companies like ArcelorMittal focus on sustainable steel production techniques.
The results include lower emissions and improved resource use.
The Role of Metallurgical Engineers in Material Processing
Fundamentals of Metallurgical Engineering
Metallurgical engineers play a crucial role in material processing.
They specialize in extracting metals from ores and developing new alloys.
Furthermore, they study the properties and behaviors of metals and alloys.
Process Optimization Techniques
Engineers utilize various techniques to optimize resource usage.
Unlock Your Career Potential
Visualize a clear path to success with our tailored Career Consulting service. Personalized insights in just 1-3 days.
Get StartedOne common method is melt processing, which enhances material properties.
Additionally, they perform alloy design to improve performance characteristics.
Process simulations also aid in predicting outcomes and refining processes.
Energy Efficiency Measures
Energy efficiency is vital in metallurgical processes.
Engineers implement technologies to reduce energy consumption.
For instance, using electric arc furnaces minimizes energy waste.
Moreover, innovative cooling techniques further enhance efficiency.
Recyclability and Environmental Impact
Recycling is a fundamental consideration in metallurgy.
Engineers focus on developing processes that enable metal recovery.
They assess the environmental impact of materials and processes.
Through life cycle analysis, they identify areas for improvement.
Collaboration with Other Disciplines
Metallurgical engineers often work alongside other professionals.
Their collaboration with chemists leads to improved processing methods.
Working with mechanical engineers enhances product durability.
This multidisciplinary approach fosters innovation and efficiency.
Techniques for Reducing Material Waste in Metallurgy
Implementing Advanced Recycling Practices
Metallurgical engineers focus on maximizing material recovery in recycling processes.
For instance, companies like Green Metal Solutions employ state-of-the-art sorting technologies.
These technologies help separate valuable metals from waste efficiently.
Moreover, engineers analyze the metal composition to enhance recycling efficiency.
By optimizing the recycling chain, they reduce the need for raw materials.
Enhancing Process Control
Effective process control minimizes waste generation throughout production.
Engineers use automated systems to monitor key parameters in real time.
For example, temperature and pressure adjustments prevent defects in metal production.
As a result, fewer materials are discarded during the manufacturing process.
Additionally, this practice extends the lifespan of equipment, reducing overall waste.
Adopting Lean Manufacturing Techniques
Lean manufacturing principles emphasize waste reduction at every stage of production.
Metallurgical engineers apply methods like value stream mapping to identify inefficiencies.
By streamlining operations, they focus resources on value-added processes.
This approach significantly lessens material waste and improves productivity.
Furthermore, organizations foster a culture of continuous improvement to maintain these benefits.
Utilizing Innovative Materials
Engineers explore alternative materials that promote sustainability.
For instance, using lightweight alloys can result in less material usage.
Such materials maintain structural integrity while minimizing waste.
Additionally, innovations like 3D printing allow for precise material utilization.
These technologies support the creation of complex components with minimal waste.
Collaboration with Suppliers
Collaboration with suppliers fosters a circular economy in metallurgy.
Engineers engage with suppliers to establish sustainable supply chains.
This partnership helps optimize material flows and minimize excess inventory.
By leveraging supplier expertise, companies enhance resource efficiency overall.
Moreover, this strategy encourages the development of recycled material sources.
Find Out More: The Future of Chemical Engineering in Canada
Innovative Recycling Methods for Metal Resources
The Importance of Recycling
Recycling metals significantly reduces environmental impact.
It conserves natural resources and energy.
Moreover, it minimizes waste in landfills.
Advancements in Recycling Technology
Modern recycling facilities employ advanced methods.
These techniques enhance efficiency and quality.
Additionally, automation systems streamline operations.
Hydrometallurgical Processes
Hydrometallurgy extracts metals using aqueous solutions.
This method is efficient for low-grade ores.
It minimizes energy consumption compared to traditional methods.
Pyrometallurgical Techniques
Pyrometallurgy involves high-temperature processing.
This technique is useful for metal recovery.
It efficiently separates metals from impurities.
Case Studies of Successful Recycling Initiatives
Many companies showcase successful recycling efforts.
For example, EcoMetal Innovations recycles copper cables effectively.
Their process reduces waste and generates revenue.
Aluminum Recycling at Global Recycling Corp
Global Recycling Corp specializes in aluminum recovery.
They produce high-quality aluminum ingots from scrap.
This significantly cuts down on energy usage.
Challenges in Metal Recycling
Despite progress, challenges remain in recycling.
Contamination of scrap materials complicates processes.
Additionally, market fluctuations impact profitability.
Strategies to Overcome Challenges
Investing in education improves recycling practices.
Public awareness campaigns can enhance participation.
Moreover, robust policies can stabilize markets.
Explore Further: Common Challenges Faced by Chemical Engineers
Energy Efficiency Practices in Metallurgical Processes
Introduction to Energy Efficiency
Energy efficiency plays a vital role in metallurgical engineering.
It improves sustainability and reduces operational costs.
Furthermore, it lowers carbon emissions significantly.
Advanced Technologies for Resource Optimization
Metallurgical engineers utilize advanced technologies to enhance processes.
Automation systems, for example, streamline operations effectively.
These systems monitor energy use and adjust accordingly.
Moreover, integrating artificial intelligence optimizes decision-making.
Process Modification Techniques
Engineers modify existing processes to increase energy efficiency.
One common method involves redesigning furnace systems.
Implementing regenerative burners can dramatically cut energy usage.
Additionally, they use waste heat recovery systems.
This process recaptures heat and utilizes it elsewhere.
Material Selection and Its Impact
Choosing the right materials contributes to energy efficiency.
Engineers focus on high-performance materials that require less energy.
This choice minimizes waste and enhances overall process efficiency.
Monitoring and Continuous Improvement
Regular monitoring is essential for optimizing metallurgical processes.
Engineers employ real-time data analytics for this purpose.
This approach identifies inefficiencies in energy usage quickly.
Subsequently, teams can implement corrective actions swiftly.
Moreover, continuous improvement practices drive ongoing advancements.
Case Studies and Real-World Applications
Many companies have seen significant gains from these practices.
For instance, Alnova Metals reduced energy consumption by 30%.
They implemented energy-efficient technologies across their operations.
Similarly, GreenTech Industries optimized processes for better resource management.
These case studies demonstrate the tangible benefits of energy efficiency.
Uncover the Details: The Role of Biomedical Engineers in Revolutionizing Canada’s Healthcare Solutions
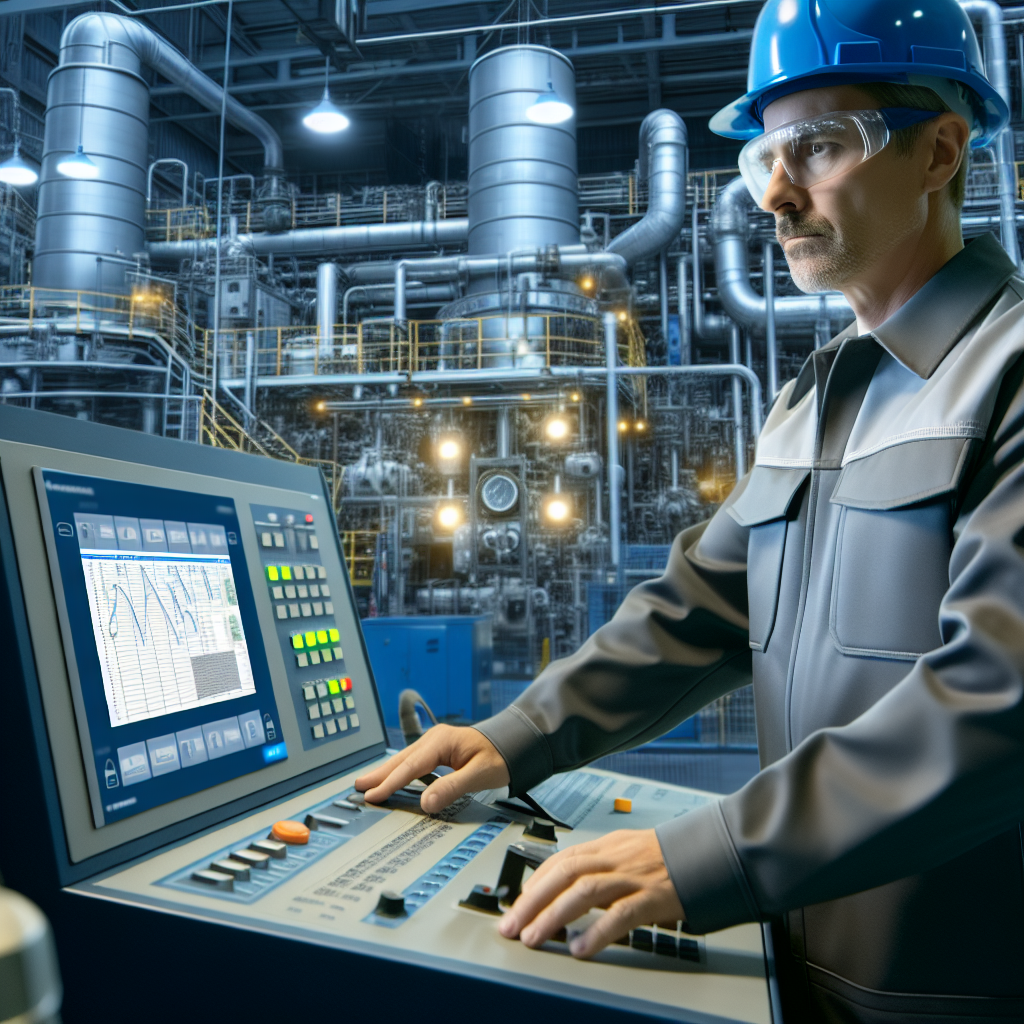
Use of Advanced Technologies for Resource Management
Introduction to Advanced Technologies
Metallurgical engineers increasingly utilize advanced technologies.
Artificial Intelligence (AI) revolutionizes resource management.
IoT devices provide real-time data for better decisions.
The Role of Artificial Intelligence
AI algorithms analyze large datasets effectively.
They help in predicting resource needs accurately.
Additionally, AI optimizes production processes continuously.
This leads to reduced waste and improved efficiency.
Benefits of Internet of Things (IoT)
IoT sensors monitor material usage remotely.
They ensure timely interventions when resource levels drop.
Moreover, IoT enhances real-time data collection.
This capability allows for proactive decision-making.
Combined Impact of AI and IoT
Integrating AI with IoT offers greater insight into operations.
Companies can make informed adjustments quickly.
This synergy leads to significant cost savings.
Furthermore, it promotes sustainable resource usage.
Case Study: Innovative Solutions in Action
Recent projects showcase successful technology integration.
For instance, a leading metals company implemented AI solutions.
They achieved a 30% reduction in material waste.
Similarly, IoT-driven monitoring improved uptime by 25%.
Future Trends in Resource Management
Emerging technologies promise to enhance metallurgical practices.
Machine learning will further refine predictive analytics.
Meanwhile, advancements in IoT will enable even smarter systems.
These trends aim to create a more sustainable industry.
Uncover the Details: Why Sustainable Engineering Jobs Are Canada’s Fastest Growing Field
Sustainability in Metallurgy: Balancing Resource Use and Environmental Impact
The Role of Metallurgical Engineers
Metallurgical engineers play a crucial role in optimizing resource usage.
They employ innovative techniques to enhance material efficiency.
Furthermore, they focus on reducing waste throughout production processes.
These engineers analyze the entire lifecycle of materials to minimize impact.
Techniques for Resource Optimization
Advancements in technology enable metallurgical engineers to improve resource utilization.
For example, they utilize advanced modeling software for process simulations.
Such simulations allow for accurate predictions of material requirements.
Moreover, engineers implement recycling processes to reclaim valuable materials.
Implementing Sustainable Practices
Sustainability requires integrating eco-friendly practices into engineering workflows.
Engineers often use sustainable materials in product design.
They also prioritize energy efficiency in metallurgical operations.
As a result, companies can reduce their carbon footprints significantly.
Collaborating with Industries
Collaboration between metallurgical engineers and industries enhances sustainability efforts.
For instance, partnerships with recycling firms optimize material recovery.
Additionally, sharing knowledge with manufacturers fosters innovative solutions.
Such cooperation can lead to industry-wide standards for more sustainable practices.
Regulatory Compliance and Certification
Compliance with environmental regulations is crucial for metallurgical operations.
Engineers stay informed about local and international standards.
They work to ensure that processes meet or exceed these guidelines.
Obtaining certifications also helps companies demonstrate their commitment to sustainability.
Future Trends in Metallurgy
The future of metallurgy will likely focus on continued resource optimization.
Engineers will further explore alternative materials and innovative processes.
Technologies such as artificial intelligence may streamline operations even more.
Ultimately, these advancements will contribute to a more sustainable metallurgical industry.
Case Studies of Successful Resource Optimization in Metallurgical Industries
Innovative Smelting Techniques
ABC Metals implemented innovative smelting techniques to enhance resource efficiency.
By introducing electric arc furnaces, they reduced energy consumption significantly.
This shift enabled them to recycle scrap metal more effectively.
Consequently, they achieved a 30% reduction in raw material usage.
Advanced Alloy Development
XYZ Alloys focused on advanced alloy development to optimize resources.
Utilizing computer simulations, they designed alloys with superior properties.
These customized alloys reduced waste during the manufacturing process.
As a result, production costs decreased while performance improved.
Process Automation and Control
DEF Industries adopted process automation to refine their operations.
Automated systems provided real-time data, enabling quick adjustments.
This capability minimized material waste significantly.
Moreover, it enhanced overall product quality and consistency.
Collaboration with Research Institutions
LMN Corporation collaborated with universities for resource optimization research.
They developed methods to extract metals from complex ores sustainably.
These partnerships yielded innovative approaches to waste reduction.
In turn, the company improved its recycling rates by 40%.
Employee Training and Engagement
OPQ Group invested in employee training programs focused on resource efficiency.
Workers learned techniques to identify and minimize waste in production.
This initiative resulted in a culture of continuous improvement.
Engaged employees contributed significantly to reducing resource consumption.
Additional Resources
What’s your starting salary and engineering job, and what would you …
Study Metallurgical Engineering For Students in Abroad – Karan …